10 Biggest Facilities Management Challenges and the Cost Struggle
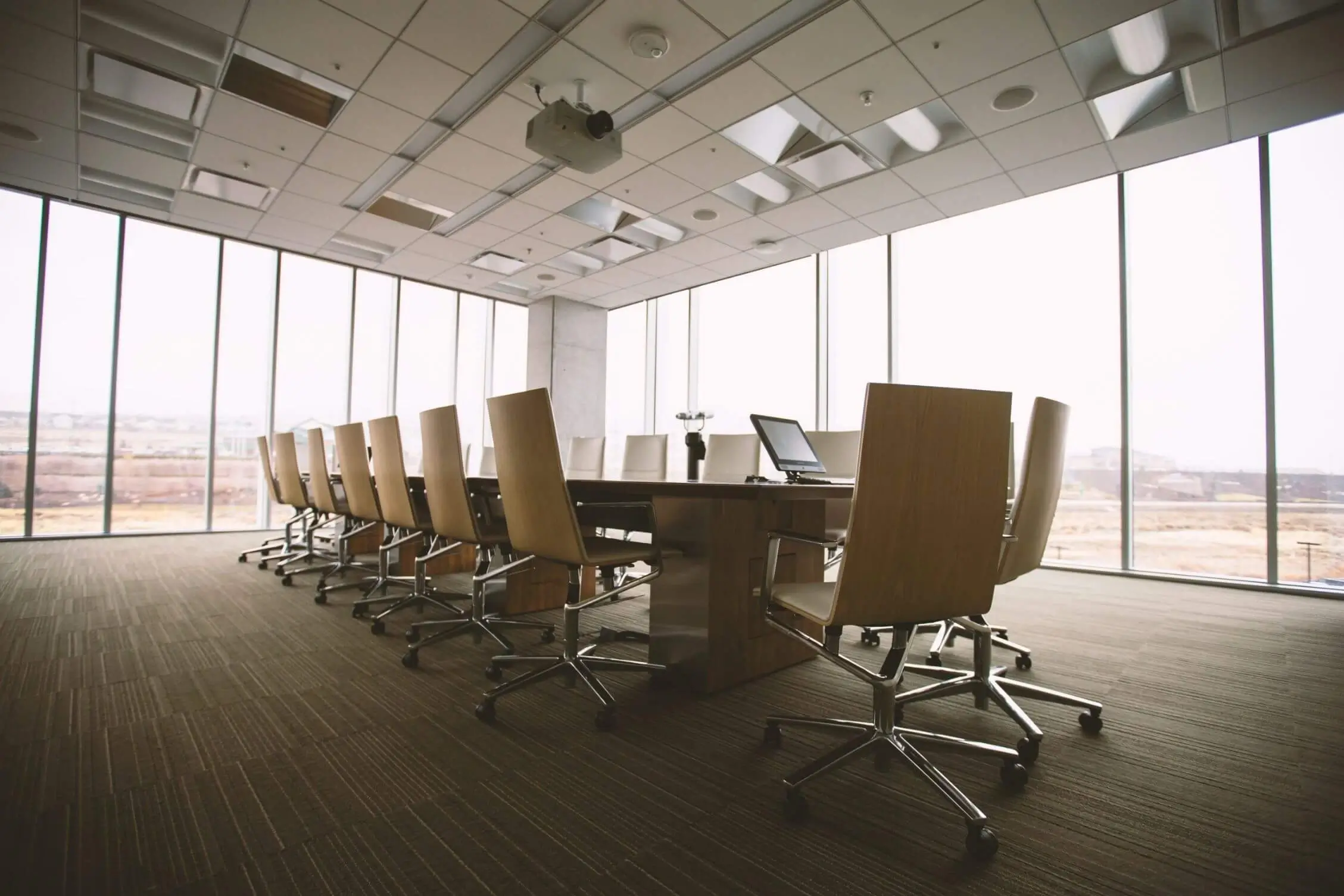
Often people are ignorant of this fact but successfully steering facilities and managing operations is full of challenges. Despite all the ambition to succeed, facilities struggle woefully to strike budget and cost balance. In this article, we are going to look at some of the biggest issues and struggles faced by facilities, why they face it and the solutions.
The cost of labor, material and supplies, energy, and government taxes, consume a substantial portion of spending in facilities. Utility costs are on the rise, and facilities need to consistently keep a watch on their operating costs, as going unmonitored they start eating into profits, thereby drastically affecting the bottom line.
This post covers challenges faced by facilities management leaders that end up impacting their budget, costs, and, in some cases, margins—making it essential to adopt facility management best practices to minimize risks and drive operational efficiency. Let’s dive in-
Biggest Facilities Management Challenges and the Reasons Why Facilities Struggle with Costs
Understanding what’s causing your facility to overspend or why budgets are failing is critical important to put you in a better position to address issues proactively. The underlying assumption most times is that cost is an efficiency problem, but that’s not always the case. As you will see the issues and challenges facilities face are internal as well as external, and involve many stakeholders.
Poor productivity and inability to identify the root causes
Monitoring a single or select few parameters do not provide a comprehensive picture of facilities performance. In order to convert pain points into opportunities, facility managers must invest quality efforts to identify problem causes. A well-managed facility thus requires a holistic insight into the performance of the entire system.
Concerning employees, machines, processes, and infrastructure, there can be scores of facility-related issues that can hamper productivity. The productivity is derailed to an extent that reversing to normalcy becomes a herculean task. In the absence of a monitoring system, one cannot identify root causes, and the problem continues to escalate. The slowdowns ultimately cause a ripple effect throughout the value chain and bring the business under its grip.
Also read:What is integrated facilities management
Lack of transparency keeps hurting
Transparency is linked to performance. It helps control costs, maintain service quality, and meet compliance. Here, we understand how the lack of transparency at two important levels can take a toll on business productivity and thereby on the bottom line.
People and Process
Non-transparency creates a scope for the facility staff to manipulate crucial people performance metrics such as job completion status, service efficiency, and average response time, which in the long run affects customer sentiments and leads to poor customer service. Lack of visibility creates a trail of sub-standard operations that transfer from people to processes which distorts the entire operation.
As per MIT Sloan’s research, customers are willing to pay 2%-10% extra to companies that offer greater visibility into their operations. Reversely, when people and processes lack transparency, customers grow hesitant of maintaining relations with the company.
Vendors
Fragmented and inconsistent processes are a direct result of not observing transparency. In a similar vein, non-transparency between subcontractors/suppliers and the company proves detrimental to business prospects. Harvard Business Review Analytic Services for Basware has unearthed that nearly 60% of business leaders expressed that lack of transparency invites significant risks for the company.
The following are the areas where vendors have the scope for manipulation when facility leaders fail to make them transparency-compliant:
- Safety procedures
- Raw material sourcing processes
- Service/product quality
- Labor practices
- Environmental sustainability
Inefficiencies – in processes and people
Lack of transparency does adversely impact performance. However, that’s just a small part of the problem, as there are myriad factors that facilities have to consider when it comes to efficiency.
As much as 75% of all failures in critical facilities are caused by human errors, and turning a blind eye can cascade the faults into an unmanageable operational issue.
As mentioned earlier, real-time visibility into process and manpower performance is important, or else inefficiencies start creeping in and some of the reasons that contribute to it include:
- Not establishing performance metrics or not monitoring them.
- Non-monitoring of asset performance – asset utilization (overutilization/underutilization), asset turnover, and asset failure.
- Not keeping track of random and routine incidents.
- Remaining unaware of maintenance spend and lost operations times
- Non-monitoring of employee metrics like accident rates, absence rates, and employee turnover rates.
Inability to identify process waste
How to identify waste remains a mind-boggling question facing many facilities, as the possibilities are limitless. A mere intention to reduce waste produces no consequence if the business doesn’t understand how to recognize waste and eliminate it. Surprisingly, this is a facility industry challenge not many leaders focus on.
As per Lean practices, the common process wastes in facilities include unnecessary motions, unneeded inventory, slow material movement, and poor process designs.
Lacking capabilities to build Lean practices and conducting waste analysis are two key steps that prevent facilities from eliminating process waste. Moreover, the one-fits-all approach doesn’t work with process waste as each waste type will require a bespoke approach to address it.
Hidden costs eat into profits
When periodically analyzing costs, you must take a closer look at the following elements:
- Emergency repairs: Costs consumed by unplanned maintenance activities.
- Asset life: Assets function for a shorter than expected span.
- Equipment efficiency: Higher than expected energy consumption by the equipment.
- Safety: Following poor safety practices result in incurring extra costs for incident and hazard management.
- Vendor Management: You fail to quantify the ROI against the fees you are paying to vendors.
- Hourly rates: You fail to take a closer look at per-hour trip charges, material and labor costs, and freight.
- Compliance: Non-adherence to standards and policies result in fines.
The common mistake profit-losing facilities commit is that they do not recognize the importance of getting a deep dive into these elements. Going unmonitored, these elements stealthily consume your budget and adversely impact profits in the long term.
Lack of analytics vision
“Today, any facilities manager looking to stay on top of his/her game, needs to be increasingly data-driven. The profession is moving away from simply being a reactive, dispatcher of technicians for work requests,” notes David Markowitz, a communication professor at the University of Oregon.
“We can interpret the enormous power data analytics offer for building a sustainable, high-performance facility. However, remaining distant from predictive capabilities makes facilities stagnant. For instance, if you take the coliving sector, absence of data-driven operations will slowly drain your profitability and by the time you realize the full picture you would have suffered a lot. Such a stagnancy is contributed by the following factors:”
- Data literacy: There’s weak data literacy amongst leaders.
- Data quality: Data is not worth deriving value from, and executives don’t have faith in it. There is no single version of the truth, as data is siloed across functions and difficult to access.
- Tool Capabilities: Even after investing in analytics platforms, the challenge of developing strong skills in a shorter span of time keeps haunting executives.
- Resources: There are no sufficient resources to streamline analytics across processes.
- Change management: Top management is not willing to adopt a data-driven culture
When facilities fail to leverage analytics capabilities, they witness the resultant impact in the form of higher costs, escalated resource use, and frequent equipment failures—undermining core goals tied to facility management and sustainability.
Not learning from poor KPI scores
Increasingly, there has been a lot of focus and emphasis on monitoring KPIs across processes and functions in the facilities industries. And yet, when it comes to taking decisitive action or making those KPIs insights actionable, facilities management teams find themselves struggling many times. Measuring performance poorly i.e. not taking actions using those insights can come with awful consequences on cost front. Some examples of poor KPIs include:
- Bad first-time fix rate: Operators make multiple visits to repair the same asset/equipment. It is a clear indicator of non-performing teams and poor customer service.
- Higher number of repeat visits: It is directly correlated to a bad first-time fix rate and a poor figure denotes poor customer service.
- High average time and cost: Vital for scheduling and measuring the field service team’s performance, high average time and cost are indicators of overutilization of time and cost.
- Low technician utilization: Your technicians are spending more time on paperwork or in transit activities as compared to spending efforts on the core activities.
- Revenue leakage: It occurs due to non-billing or under-billing that fails to catch your notice which causes a reduction in revenue.
- Low service profitability: The revenue generated is not par with the expectations, resulting in lower than targeted profitability.
Failure to identify pilferages
Leaders need to be attentive to the menace of pilferages that stealthily eat away revenue. The impact of these attritional losses can be massive as along with causing loss of inventory, they can increase security costs and also result in loss of customer trust.
Pilferages are usually associated with inventory, caused by unauthorized actions during the course of its journey in the value chain. However, spare parts, consumables, and all goods that facilitate operations can be pilfered. Here are the areas where most instances of pilferage occur:
In-transit pilferages
It happened that in 2011, a driver of a transportation service provider reached a distribution centre in Ontario, California. The contract for loading was obtained by the driver from an online platform. However, after the trailer was loaded and the driver departed, only to be not seen again.
The incident highlights how facilities management might not account for in-transit pilferages, however, the above episode sheds light on how the absence of verification mechanisms at facilities can result in in-transit pilferages.
Warehouse pilferages
What if pilferages occur where they are in the custody of those who are responsible for safeguarding them? Warehouse pilferages are caused by poor storage practices or inventory theft at warehouses. The theft can be committed by warehouse supervisors by colluding with external parties.
Store pilferage
Common in the retail industry, store pilferages can bring a heavy burden on facility managers when left unmonitored. Operating a retail store is a highly complex job. Not just the merchandise but even every transaction is a potential source of revenue pilferage.
Hiring challenges
Hiring the best talent can be one of the biggest challenges of facilities management when there is no dearth of opportunities for experienced professionals. What lands businesses into this challenge is the failure to retain good employees.
As per Alana Dunoff, a facility planner veteran, cross-training can prove helpful in retaining employees, and encourage them to remain bonded with the business.
The challenge is most people leave without transferring knowledge, which means you need to train new hires – again you need to inflate your time and cost budget.
The complex hiring cycle, lack of resource pool, and the need to go to places to hire trained professionals are some factors that make hiring a challenging exercise for facilities. The hiring overheads can thus snatch away a good portion of revenue.
Overwhelming technology and change
“Digital transformation requires a jump on the technology side, but it requires a leap on the people side,” says Bill Gundrey, executive director for digital engineering and operations at Raytheon Missiles & Defense.
So, bringing changes in the attitude of team members is as important as thinking about adapting to ongoing innovations. Not lacking a vision can be a threat, but having a vision and not leveraging it for advantage due to a rigid mindset can be the biggest blockage for facilities.
To give an example, in general, 79% of businesses now see predictive maintenance as the most important application of industrial data analytics. So, the move towards IoT, AI, and Cloud in FM is already gaining momentum. Facilities that fail to recognize these advancements will fall behind in the race. change the mindset is one of the biggest obstacles in implementing CAFM and other important technologies that aid facilities.
It’s never too late until you act well in time
When facilities act with a lackadaisical attitude, they end up building a precarious foundation. It’s high time that facilities leaders understand the importance of digital enablement for preventing the erosion of revenue. Building and deploying advanced facility management software can help achieve many goals in a single stroke.
Last but not the least, imperfection may be acceptable; however, not acting in time will never be. It’s never too late to make a new beginning, but you need to identify the points where shifting gears becomes essential. You must know how facilities management trends are shaping the industry and adapt to changes fast. To build profit-centric strategies, start embracing the change from today itself.