What Is Time-based Maintenance (TBM)? Everything You Must Know
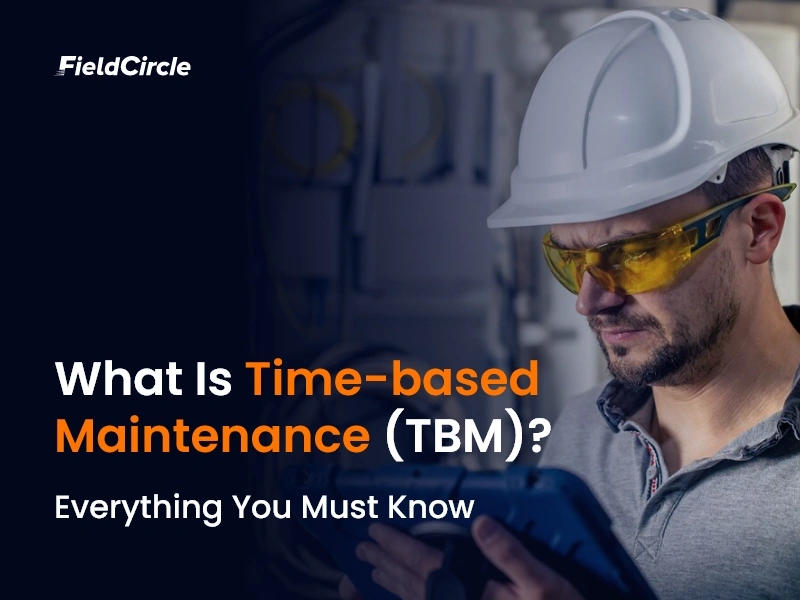
Time-based maintenance is a maintenance strategy where equipment is serviced at regular intervals, based on a set schedule. Because of this approach, assets are maintained according to a set schedule and there are no unexpected breakdowns. A defining feature of TBM is its proactive nature, where equipment receives the necessary care at the right time, even if it’s not currently showing signs of wear.
Large organizations such as Ford, General Electric, Delta Air Lines, McDonald’s, and ExxonMobil have successfully relied on TBM to maintain smooth operations. For instance, airlines follow TBM schedules for engine overhauls based on flight hours, with regular checks after a specific number of flight cycles, such as every 1,000 hours for smaller components or every 5,000 hours for major parts.
Similarly, shipping companies like Maersk maintain their vessels using TBM schedules, performing inspections and repairs based on predefined time intervals, such as annual dry-docking or periodic maintenance every few months.
While the method is effective in many scenarios, it also presents challenges that maintenance teams must navigate. We’ll explore these challenges and best practices for successfully implementing TBM in the following sections.
How Does Time-Based Maintenance Work?
The following is a detailed workflow outlining the process of time-based maintenance, highlighting each key step:
- Set Maintenance Schedule: Establish time intervals (e.g., daily, weekly, monthly) based on manufacturer recommendations or historical data.
- Plan Activities: Identify the tasks required for each scheduled maintenance period (e.g., cleaning, lubrication, inspections).
- Perform Maintenance: Carry out the maintenance activities on equipment or machinery according to the set schedule, regardless of current operational conditions.
- Document Work: Record the maintenance work performed, including time, resources used, and any issues noted.
- Evaluate and Adjust: After a few cycles, evaluate the maintenance schedule for efficiency and adjust if needed, based on performance data or changing operational conditions.
What are the Benefits of Time-based Maintenance?
Time-based maintenance (TBM) offers several benefits seen in shutdown reduction, simplicity of implementation, streamlined processes, systematic schedules, compliance to warranties, equipment lifespan enhancement, and ability to operate within budgets. We touch upon diverse examples to illustrate how these benefits are realized through TBM.
-
Keep Unexpected Shutdowns at Bay
-
Run Maintenance Without Fancy Tech
-
Avoid Maintenance Overload and Last-Minute Scrambles
-
No More Guesswork with Spare Parts
-
Stick to Warranty and Legal Requirements Without Hassle
-
Push Equipment Lifespan to Its Limit
-
No More Budget Surprises
Unplanned failures disrupt operations, causing productivity losses and unnecessary repair expenses. One way to prevent these issues is by adhering to fixed servicing schedules. By following a time-based maintenance approach, businesses can address wear and tear before it becomes a major problem.
For example, in rotating machinery, components like bearings naturally wear down due to friction, and lubricants degrade over time. Without a maintenance schedule, these issues can lead to increased resistance, excessive heat buildup, and premature failure. Regularly replacing degraded lubricants before they cause significant damage ensures that machinery operates smoothly without unexpected interruptions.
In electrical systems, components like capacitors degrade and affect voltage stability. Time-based replacements of these parts help prevent minor issues from escalating into major system failures, thus optimizing costs and maintaining reliable performance.
Overall, with routine servicing, hidden deteriorations are identified early, and operations run smoothly without sudden breakdowns or unforeseen repair costs.
Not every facility runs sophisticated condition-monitoring sensors, and not every machine needs them. Time-based maintenance operates without relying on vibration analysis, infrared thermography, or oil particle counting. It works as a fixed maintenance plan.
Instead of tracking real-time data, servicing follows a set schedule based on historical failure patterns. For instance, when hydraulic systems accumulate debris in filters, it leads to pressure drops. Changing filters at fixed intervals keeps flow rates steady without needing real-time clogging detection.
Likewise, gears in heavy-duty equipment experience metal fatigue as they develop micro-cracks over time. Replacing them before they fail eliminates the need for continuous stress monitoring. Maintenance crews focus on pre-planned servicing rather than chasing sensor alerts, and for all this they don’t always need sophisticated toolsets.
Workloads spike when teams handle maintenance reactively and as a result, they are forced to juggle emergency repairs with routine upkeep. With a schedule, the team spreads work evenly, which keeps crews from running ragged one month and twiddling their thumbs the next.
Let’s take the case of heavy machinery like CNC machines which requires coil cleaning, fan inspections, refrigerant level checks, component alignments, and calibration from time-to-time.
However, when servicing gets pushed back, minor inefficiencies stack up, and multiple units are forced into unplanned downtime at the worst possible time.
Assigning these tasks to fixed slots prevents maintenance technicians from dealing with multiple urgent failures at once. Steady workloads keep technicians from getting swamped while keeping everything in working order.
Waiting for a component to fail before ordering a replacement leads to unnecessary downtime. Across the set-up, wear and tear happens continuously, and the need for spare parts is quite but obvious. Like, diesel engines have fuel injectors that degrade and if injectors are not available then it impacts combustion efficiency.
As Time-based maintenance schedules part replacements ahead of time there remains no scope for stock shortages. So, when fuel injectors go out of order, swapping them on a set schedule eliminates performance dips caused by clogged nozzles.
Similarly, conveyor belts stretch and crack over months of continuous use, and they require periodic replacements to avoid abrupt failures. When replacements are planned, procurement teams secure stock without last-minute rush orders.
Without structured scheduling, businesses would end up scrambling for urgent shipments, paying premium prices for expedited deliveries. On the other hand, planning ahead keeps operations running smoothly while keeping procurement costs in check. The approach also boosts predictive maintenance as the conditions on which anticipations are made are always ideal.
When it comes to equipment and machinery, manufacturers and regulatory agencies set strict maintenance guidelines to protect both the business and the customer. Ignoring these scheduled intervals lead to serious consequences voiding warranties and triggering costly legal disputes.
One common scenario here is about industrial boilers, which must undergo inspections every few months for operations to remain safe. If the business fails to follow the required schedule, not only does it face operational hazards, but the manufacturer also refuses to cover any repair costs when an untoward incident takes place.
If we consider the automotive sector, vehicle fleets require regular servicing according to manufacturer recommendations. For instance, specific parts must be charged at pre-determined mileages. In the event these servicing dates are missed, apart from leading to mechanical failures it also leads to the manufacturer refusing to honor warranties.
In essence, by adhering to the prescribed maintenance intervals, companies don’t just avoid expensive breakdowns. They also safeguard themselves from potential legal headaches and keep their warranties intact, so that they don’t have to foot the bill for avoidable repairs.
In restaurant kitchens, commercial kitchens are maintenance-heavy machines. Over time, the condenser coils accumulate dust, and if they aren’t cleaned regularly, the compressor has to work harder, leading to overheating and eventual failure.
To make the refrigerator operate efficiently for years, you need to set a cleaning schedule and avoid the need for premature replacements or costly repairs. You can always streamline the process with a dedicated kitchen maintenance application.
The reason we highlighted this example is that the same principle applies to all machinery. So you cannot defer or skip maintenance, because may it be any machine, components age faster and fail unexpectedly, possibly also before their true service life should end.
Time-based maintenance is a panacea here as it replaces necessary parts at scheduled intervals, and prevents the slow, unnoticed wear that causes failure.
We understand through another notable example which of heavy-duty pumps in industrial settings. These pumps rely on seals to prevent leaks and maintain pressure. Over time, these seals degrade and, without regular replacements, leaks become a serious problem, drastically reducing the pump’s efficiency and lifespan.
When you follow scheduled maintenance, you swap out seals before they begin to fail, and the pump continues operating at optimal levels for much longer, thus avoiding the operational disaster.
Consider the following situations where maintenance is essential:
- Cooling systems in data centers require regular filter changes to avoid overheating.
- Commercial HVAC systems need periodic checks to ensure proper airflow and temperature regulation.
- Forklift fleets require battery maintenance to extend equipment lifespan and improve service efficiency. This is important in industries like manufacturing where time-based maintenance can replace batteries in time and prevent downtimes.
- Warehouse lighting systems needing scheduled bulb replacements to maintain efficiency and safety.
- Heavy-duty compressors require valve replacements after a certain number of operational hours.
- Manufacturing plants rely on hydraulic presses that need periodic fluid changes to maintain optimal pressure levels.
Think about the costs businesses have to incur if maintenance for the above scenarios doesn’t take place in time. It will disrupt the budget and spoil the financial planning.
The unpredictability of these emergencies makes it difficult to allocate resources efficiently, which could be anything like urgent service fees, and this will inflate maintenance costs.
Timely maintenance provides enough room to businesses to anticipate necessary repairs and allocate funds accordingly, and thus eliminate financial surprises. Since the frequency and severity of major repairs is reduced and maintenance expenses are both predictable and manageable, it allows businesses to control their budgets.
Challenges of Time-based Maintenance and Their Solutions?
Before you avail the benefits discussed above, you should be capable of dealing with the following challenges that time-based maintenance poses.
1. Arbitrary Temporal Intervals
Maintenance is based on time, not actual wear. Some parts get serviced before necessary, while others, used more, risk failure before the next check, leading to inefficiency.
Solution: Implement condition-based monitoring to service parts only when their performance or wear shows signs of degradation.
2. Disruptions from Rigid Operational Alignment
Scheduled maintenance doesn’t align with production cycles, causing unnecessary downtime. Moreover, adjusting schedules is tough, leaving no room for flexibility and forcing halts even when equipment is fine.
Solution: Introduce predictive maintenance strategies to align maintenance with equipment usage patterns, minimizing downtime.
3. Excessive Inventory Burden from Predictable Replacements
Pre-planned servicing requires stocking parts that may never be used, which may lead to excess inventory and higher storage costs. Teams have to keep an eye on whether unused parts are taking up space.
Solution: Adopt a just-in-time inventory system that orders parts based on real-time need rather than pre-scheduled replacements.
4. Premature Interventions Undermining Component Longevity
Routine maintenance may occur early for some parts which might still be in good condition. As parts are replaced or adjusted before needed, they may be exposed to risks that reduce their lifespan and reliability.
Solution: Use data-driven diagnostics to ensure parts are only serviced when truly necessary, extending their functional lifespan.
5. Workforce Saturation from Unvarying Maintenance Cycles
Fixed schedules lead to maintenance teams working on low-risk assets unnecessarily, and it wastes time and causes fatigue. Skilled workers may thus get distracted from more urgent tasks.
Solution: Shift to a flexible, demand-driven approach, prioritizing high-risk assets and optimizing workforce utilization.
6. Reliability Perception Masking Emerging Issues
Scheduled servicing creates a false sense of reliability and teams may be forced to overlook small issues between maintenance intervals. In this process, minor problems can escalate into failures if left unaddressed.
Solution: Implement continuous monitoring and early warning systems to detect emerging issues before they lead to failures.
When to Use Time Based Maintenance?
These are the various scenarios where time-based maintenance is an effective strategy for managing equipment upkeep:
- Routine equipment checks: Regular maintenance helps ensure that machines like motors or pumps are inspected after a set number of hours, preventing unexpected failures by addressing wear and tear early.
- Scheduled part replacement: By setting fixed intervals for part replacements, such as air filters or belts, equipment performance remains optimal, and costly breakdowns are avoided by replacing components before they fail.
- Seasonal equipment readiness: Maintenance before peak usage periods—like for lawnmowers or snowplows—keeps equipment running smoothly during busy seasons, ensuring they are fully operational when needed.
- Preventing wear and tear: Regular checks for outdoor equipment exposed to harsh elements help catch issues like corrosion or environmental damage, preventing more serious damage from developing.
- Calibration of instruments: Recalibrating precision instruments like thermometers or scales at set intervals ensures they remain accurate, preventing measurement errors that could affect operations.
- Backup system testing: Testing and maintaining backup generators or UPS systems at regular intervals ensures they’re ready to perform when needed, even if they’re not used frequently.
- Safety equipment checks: Regular inspections of fire alarms and emergency lighting help guarantee that safety systems are always functional and compliant with regulations, reducing the risk of failure during emergencies.
- Battery management: Scheduled checks and replacements for batteries in backup power systems ensure they’re fully charged and ready to perform when required, avoiding power loss during critical situations.
Who Utilizes Time-Based Maintenance?
These are the various stakeholders, across different industries and sectors, who benefit from using time-based maintenance strategies to maintain their equipment and ensure operational efficiency:
- Manufacturers: Factories and production lines implement time-based maintenance to keep machinery operating efficiently, preventing production delays due to equipment failure.
- Fleet operators: Businesses with vehicle fleets rely on time-based servicing to maintain trucks, cars, and other vehicles, ensuring they remain roadworthy and minimize costly repairs.
- Facility managers: In building maintenance management, managers follow time-based schedules to service HVAC systems, elevators, and lighting, preventing issues that disrupt day-to-day operations.
- Power plant operators: Time-based maintenance is essential for operators in power generation, helping to keep turbines, boilers, and generators in working order and avoid unscheduled outages.
- Healthcare providers: Hospitals and clinics schedule regular maintenance on medical equipment like MRI machines, infusion pumps, and ventilators to guarantee safe, uninterrupted use.
- Farmers: Agricultural businesses with heavy machinery use time-based maintenance to ensure tractors, harvesters, and irrigation systems run smoothly during peak growing seasons.
- Construction firms: Construction companies schedule routine checks and servicing of machinery such as cranes and bulldozers, preventing equipment failures during critical project timelines.
- Aviation companies: Airlines perform time-based maintenance on aircraft, ensuring that planes are inspected and serviced after specific flight hours or time intervals to meet safety regulations.
Difference Between Time-Based Maintenance and Condition-based Maintenance
Both time-based maintenance and condition-based maintenance have their own relevance in maintenance management. Below, we discuss how these two types of maintenance strategies differ by comparing them across different parameters.
Parameter | Time-Based Maintenance (TBM) | Condition-Based Maintenance (CBM) |
---|---|---|
Timing / When to Use |
Maintenance tasks are scheduled at fixed intervals (e.g., daily, weekly, monthly). |
Maintenance is performed based on the actual condition or performance of equipment. |
Cost |
Generally lower upfront cost due to fixed maintenance schedules. However, it can be inefficient as parts are replaced even if they are not worn out. |
Potentially higher upfront costs due to monitoring equipment, but can be more cost-effective in the long run by reducing unnecessary repairs. |
Flexibility |
Low flexibility. Maintenance is scheduled regardless of the actual condition of the equipment. |
High flexibility. Maintenance is only performed when the equipment’s condition requires it, potentially saving resources. |
Risks of Unplanned Downtime |
Higher risk of unplanned downtime as maintenance might be missed if schedules are not strictly followed. |
Lower risk of unplanned downtime since maintenance is triggered by real-time equipment data, preventing unexpected failures. |
Efficiency |
Lower efficiency, as maintenance is done at fixed intervals regardless of need, often leading to wasted resources. |
Higher efficiency, since maintenance is only carried out when the equipment shows signs of wear or failure. |
Resource Utilization |
Maintenance resources (e.g., labor and parts) are used on a regular basis, even when not necessary. |
Resources are used only when needed, leading to more effective allocation of labor and materials. |
Predictability |
Highly predictable as maintenance is done at fixed intervals. |
Less predictable, as maintenance is performed based on the health of the equipment, which can vary. |
Equipment Lifespan |
May reduce equipment lifespan if parts are replaced too early or too frequently. |
Potentially extends equipment lifespan since maintenance is done based on real usage and wear. |
Data Dependency |
Little to no reliance on data. Maintenance is performed according to a pre-set schedule. |
Highly data-dependent. Requires sensors, monitoring tools, and real-time data to assess equipment condition. |
Suitability for Critical Systems |
Not ideal for highly critical systems where unplanned downtime is costly. |
More suitable for critical systems that cannot afford to break down unexpectedly, as maintenance can prevent major failures. |
Complexity |
Simple to manage, as it follows a clear schedule and does not require complex systems. |
More complex, requiring real-time monitoring systems and data analysis to determine when maintenance is needed. |
Adaptability to Changing Conditions |
Low adaptability. Maintenance is fixed and does not adjust based on operating conditions or changes in the system. |
High adaptability, as maintenance schedules can change based on real-time conditions, usage patterns, and external factors. |
Best Practices to follow when implementing Time-based Maintenance
Discussed are the best-practices which, when followed, assist businesses to effortlessly tackle the challenges we discussed and enjoy the benefits of time-based maintenance.
- Stick to a Well-Defined Maintenance Schedule
- Follow Manufacturer Recommendations
- Keep Accurate Maintenance Records
- Train Personnel Properly
- Utilize Automated Alerts for Service Dates
- Stock Up on Spare Parts
- Conduct Pre- and Post-Maintenance Inspections
- Analyze Historical Data for Optimal Service Intervals
- Rotate Tasks Among Trained Personnel
- Establish Accountability for Maintenance Tasks
- Monitor Equipment Performance Trends
- Align Maintenance with Operational Downtime
- Standardize Checklists for Maintenance Tasks
- Set Realistic Maintenance Timelines
- Review and Adjust Maintenance Schedules Periodically
- Document Deviations from the Planned Schedule
A reliable maintenance schedule is essential to avoid unexpected breakdowns and keep equipment in optimal condition. By setting a regular routine, you can ensure your assets perform efficiently over time, reducing costly downtime and repairs.
Utilizing the manufacturer’s guidelines ensures safe operation and extends equipment lifespan. Aligning your maintenance tasks with these recommendations provides the right balance of care for every piece of equipment, keeping operations running smoothly.
Accurate documentation of all maintenance activities helps in diagnosing recurring issues and supports data-driven decisions. Detailed records allow you to track repairs, parts replacements, and overall equipment performance for informed future actions.
Well-trained personnel are essential to execute maintenance tasks correctly and reduce the risk of errors. Providing team members with proper guidance and continuous training ensures all activities are performed efficiently, and equipment is well cared for.
Use a maintenance management software for receiving automated service reminders, preventing missed maintenance tasks, and keeping servicing on track. By setting up timely alerts, you help your team stay on top of upcoming tasks.
Maintaining a well-stocked inventory of spare parts prevents delays in repairs and reduces extended downtime. Having essential components on hand allows your team to fix issues promptly without waiting for parts to arrive.
Routine inspections before and after maintenance activities help catch early signs of potential issues and confirm that repairs have been completed properly. This step is vital for ensuring equipment runs smoothly and that no details are overlooked.
Reviewing historical data can help you adjust service intervals based on real equipment usage. By identifying patterns, you can fine-tune maintenance schedules to reflect actual performance, improving reliability and extending equipment life.
Rotating maintenance management duties among personnel ensures balanced workloads and minimizes the risk of oversight. This approach also prevents burnout and fosters a more consistent and thorough maintenance routine.
Clear accountability ensures that each scheduled task is completed on time and according to plan. Assigning responsibility and tracking progress helps maintain momentum and guarantees that no maintenance duties are neglected.
By regularly monitoring equipment performance, you can detect early signs of wear and address issues before they escalate into costly repairs. Tracking trends over time allows for proactive maintenance, reducing the risk of sudden breakdowns.
Scheduling maintenance during planned operational downtime minimizes disruptions to productivity. By aligning service tasks with off-peak hours, you can complete necessary maintenance without affecting daily operations.
Using standardized checklists ensures that no steps are missed during maintenance procedures. This approach guarantees consistency across tasks and prevents important details from being overlooked.
Establishing reasonable timelines for maintenance activities ensures tasks are performed thoroughly without unnecessary delays. Balancing thoroughness with efficiency helps maintain equipment performance without disrupting production.
Regularly reviewing maintenance schedules ensures they remain relevant as operational needs change. Periodic assessments help you stay aligned with evolving conditions and optimize service timing to meet current demands.
Tracking any deviations from the original maintenance plan allows you to analyze their impact on equipment performance. By documenting changes, you can refine future schedules and minimize the effect of unexpected adjustments.
Takeaway
Adopting FieldCircle CMMS software is a great step to simplify time-based maintenance. Our tool comes with many useful functionalities such as calendar-based scheduling, customizable service intervals, and automatic maintenance alerts.
With these features, a maintenance team is able to plan tasks well in advance and perfectly align maintenance activities with operational requirements.
A demo of our product will help you understand how to synchronize these features with your time-based maintenance strategy and save your valuable time and effort.