Usage-based Maintenance (UBM): Definition, Benefits and Strategies
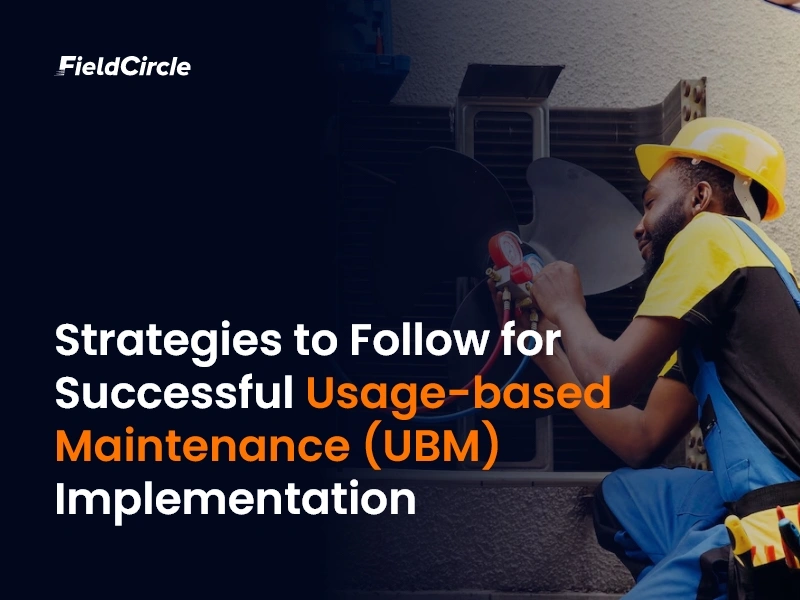
Facilities and plants have evolved and adopted new methodologies as technology facilitated such changes. One of the biggest change has been how they approach maintenance operations.
From reactive to preventive to predictive, we have made significant progress. In this transition from preventive to predictive lies a methodology that is super effective and can be implemented even when you don’t have sophisticated technologies like IoT implementation etc. for predictive maintenance operations. And that methodology is usage-based maintenance.
In this post, we will cover various aspects related to usage-based maintenance- from definition and benefits to examples and strategies. Let’s start with-
What is Usage-based Maintenance
Usage-based maintenance also known as meter-based maintenance is a type of preventive maintenance strategy that offers a smarter way to maintain equipment by focusing on how it’s actually being used, rather than sticking to fixed maintenance schedules. Instead of waiting for machines to break down, maintenance happens when it’s truly needed, based on real-time data.
But how does it help your maintenance operations? Or
What are the Benefits of Usage-Based Maintenance
As the name implies, meter-based or usage-based is directly linked to how extensive an asset or equipment has been used. And, thus it impacts the maintenance operations on various front like asset health, breakdown frequency and downtime, maintenance cost, effective resources utilization etc. Here is a list of some of the top benefits of usage-based maintenance.
Keeps Equipment and Assets Running Reliably
By servicing equipment based on real usage, chances of surprise breakdowns get reduced leading to better production and uptime.
Cuts Down on Maintenance Costs
You only do maintenance when it’s actually needed. You can also avoid regular planned maintenance based on interval and thus can save time, cost and manhours.
Schedules Work at the Right Time
You don’t need to guess anymore as the maintenance is based on real data, not just a calendar in a preplanned manner.
Extends Equipment Life
Usage based maintenance gives you an indication of when a machine needs help and that in-tun leads to better equipment health and life.
Reduces Unplanned Downtime
Since you will be observing equipments and machines based on their usage, the chances of breakdowns go down leading to less disruption and more productive time.
Smarter Use of Resources
Maintenance teams can be utilized more effectively and where they are needed instead of in a preplanned fashion. Similarly, you can improve spare parts issuance and utilization.
Better Decision-Making with Real Data
Usage tracking gives you insights on equipment performance and health that leads to better data-driven decision making.
Improves Safety and Compliance
Well-maintained equipment that are being tracked regularly for thier performance leads to improved safety and help in following compliances and regulatory requirements.
Prioritization
Heavily used equipment get more attention and are serviced more often than rarely used machines that helps in easier and more effective maintenance ops.
Supports Predictive Plans
Usage-based data lays the foundation for the future, helping identify issues before they cause problems and sets you up for future predictive maintenance roadmap.
The idea is simple— track how each piece of equipment is performing under real-world conditions and then plan maintenance around that. This way, maintenance becomes more efficient and targeted.
Strategies(Types) of Usage-based Maintenance
If you are looking to perform maintenance based on usage of the equipment and strengthen your preventive maintenance program, these are the 12 strategies that you could adopt to implement usage-based maintenance effectively to increase the reliability of your equipment and also to streamline your asset management practice.
1. Dynamic Tracking
Keeping track of equipment usage is one of the significant benefits of usage-based maintenance. Rather than waiting for a specific calendar date or a set number of hours, you collect data continuously—how many hours the machine’s been running, how much load it’s been under, and even the number of cycles it’s completed.
Sensors and IoT devices gather all of this, and the data gets analyzed to spot patterns that matter. So, when a component has been working harder than expected, maintenance teams know exactly when to jump in. It’s precise and action-driven, not based on a hunch or guesswork.
Further, real-time tracking gives you insights into the equipment’s actual performance, beyond what any generic maintenance schedule might suggest. You get a clearer picture of how different conditions affect the machinery—whether it’s high loads, frequent usage, or other stressors.
The advantage here? You spend less time and resources on maintenance that’s not needed and more time addressing the equipment that truly requires attention.
2. Threshold-Based Alerts for Critical Parameters
Set a few key benchmarks—things like pressure, temperature, or vibration—and track those in real time. When any of those parameters breach a predefined limit, an alert is triggered. It’s like having a built-in alarm system for your equipment. If something’s out of the ordinary, you’ll know right away.
Most importantly, these aren’t just random numbers, either—they’re directly tied to the equipment’s use and the load it’s under. So, if a piece of machinery is under heavy load, for instance, its temperature could rise faster than usual. An alert lets you catch potential issues before they snowball into bigger problems.
You can’t always predict when a machine’s going to hit a snag, but by keeping a close watch on those critical parameters, you can anticipate issues before they cause downtime.
These alerts aren’t just generic “something’s wrong” signals. They’re specific to your equipment’s real-world use. So, when that vibration or pressure hits a dangerous level, you can address it right away, keeping the machine running smoothly without major repairs down the line. This is a great way
3. Usage Pattern Analysis with Predictive Maintenance
Predictive maintenance is all about spotting patterns over time. By analyzing the usage data you’ve been collecting, you can start to see when equipment is likely to fail or need a tune-up. This isn’t a shot in the dark—it’s based on the real-world data you’ve accumulated.
For example, certain types of wear show up after consistent heavy use, and predictive models can use that info to forecast exactly when parts will need replacing. It’s like having a crystal ball that’s powered by data instead of magic.
What really sets predictive maintenance apart is how it gets more accurate over time. The more data you gather, the better the system becomes at recognizing trends and forecasting failures.
It’s all about making the right call at the right time. Instead of waiting until a part breaks, you can get ahead of the curve, replacing things before they fail. Implementing predictive maintenance with a CMMS is the best way to streamline the process. A computerized maintenance management system (CMMS) provides various useful predictive analytics features.
4. Load and Usage History Integration
Here’s where things get a little more granular. When you start factoring in both the load and usage history of your equipment, you’re taking a deeper dive into how it’s really performing. Let’s say you have two machines that are used for the same job, but one’s under a heavier load.
The lighter-load machine might get away with fewer maintenance checks, while the heavy-duty one needs more frequent attention. By combining both load and usage data, you can pinpoint when a machine has been pushed too hard, and you can adjust your maintenance schedules accordingly.
When you integrate this kind of data, you’re no longer guessing about what your equipment needs. If a machine’s been under heavy strain, its components will naturally degrade faster. So, by tracking how much load it’s been dealing with, you can anticipate those wear-and-tear moments.
5. Data-Driven Lubrication and Fluids Management
Your equipment works the way a vehicle works which needs the right amount of oil, coolant, or hydraulic fluid to run smoothly. But here’s the difference: with usage based maintenance, the decision to change those fluids isn’t based on a general rule; it’s based on the data you’ve gathered.
If the machine’s been working hard with heavy loads or in challenging conditions, it’ll need more frequent fluid checks or replacements. This means you’re not just following a blanket schedule, rather you’re acting based on real-time performance, and that means fewer surprises.
With this approach, you don’t waste time or money replacing fluids too early or running them down to the point of failure. Using real data from sensors, you can pinpoint exactly when those fluids are starting to degrade, and schedule replacements accordingly.
6. Automated Calibration
Automating calibration based on usage means your equipment is always in sync with its needs. Rather than waiting for scheduled calibration checks, you can set up systems to adjust automatically as equipment runs.
For example, machinery that’s under heavy use will need recalibration more frequently than one that’s lightly used. By syncing these calibrations to actual usage, you’re keeping things running without having to remember when the next manual check is due.
This system cuts out the guesswork. You don’t need to remember to calibrate after X hours of use or Y cycles. Instead, the equipment adjusts itself or triggers an automatic recalibration whenever it needs it based on actual usage patterns.
There is no human error factor and everything’s always running at optimal levels, and avoids production errors that come from miscalibrated equipment and which might unnecessarily increase the maintenance costs.
7. Proactive Wear Monitoring and Component Life Estimation
With usage-based maintenance, the wear and tear on critical components become easier to track and predict. Each piece of equipment has specific parts that will naturally degrade over time, and by using wear monitoring sensors, you can track the exact status of these components.
These sensors measure things like abrasion levels, heat, and stress on parts that are more prone to failure. By using this data, you can estimate the remaining life of a component before it reaches a critical failure point.
Instead of relying on theoretical calculations, the system provides accurate, real-time predictions on component life based on how the machine has been used. If a component is under heavier loads or higher stress than expected, its degradation will be faster. Also, replacement schedules are managed efficiently and you don’t need to over-replace parts before they truly need it.
8. Customized Maintenance Cycles Based on Intensity
When machinery is pushed harder, the wear and maintenance needs increase. A customized cycle based on intensity makes maintenance schedules more relevant here.
For instance, a machine running in light-duty mode won’t need as frequent servicing as one operating in heavy-duty conditions. By tracking usage intensity, you can schedule maintenance in direct correlation with how demanding the machine’s job is. Here, machines working harder get the attention they need without imposing unnecessary downtime on those working under less stress.
These customized cycles allow you to focus maintenance resources where they matter most. A machine that runs in demanding environments, like a factory where it’s constantly under load, will need more frequent checks and service intervals.
On the other hand, a machine operating in more controlled conditions won’t require the same level of intervention. It’s a smart and efficient approach, preventing both under-servicing and over-servicing while keeping machines operating at peak performance. In short you are saved from unnecessary maintenance requirements poking you and disrupting the entire maintenance cycle.
9. Remote Diagnostics for Instant Problem Detection
Instead of waiting for a machine to show obvious signs of trouble, remote diagnostics let you detect problems from afar in real time. Sensors on the equipment send diagnostic data, allowing technicians to analyze and diagnose issues remotely. This is especially useful in cases where immediate on-site intervention isn’t feasible.
By integrating remote diagnostics into your maintenance system, you can monitor multiple machines at once, checking their health without being physically present. Early problem detection saves both time and costs since issues are addressed before they evolve into major failures.
Notably, remote diagnostics don’t just serve as a monitoring tool. It gives maintenance teams the power to fix problems remotely or prepare in advance by understanding the issue before sending anyone on-site and this way adds another layer of efficiency to your overall preventive maintenance plan.
10. Real-Time Performance Monitoring Dashboards
Real-time dashboards give maintenance teams a bird’s-eye view of all your equipment’s health and performance. These dashboards display critical data on operating conditions, efficiency levels, and any alerts about abnormal activity.
By having all maintenance metrics in one place, maintenance teams can quickly pinpoint machines that need attention. When issues arise, whether it’s a sudden temperature rise or unexpected vibration, the team can take immediate action rather than waiting for a report or routine check.
Dashboards don’t just serve as an overview; they’re interactive and provide insights that can lead to better decision-making. Data is broken down into clear, digestible insights, so the team doesn’t have to sift through piles of raw information.
By using real-time dashboards, maintenance teams get a clearer understanding of what’s happening with the equipment at any given time. They provide a comprehensive, actionable overview that prevents critical issues from slipping through the cracks.
11. Integrated Supply Chain for Spare Parts
Usage-based maintenance works best when paired with a streamlined supply chain for spare parts. By analyzing usage data, you can predict when parts will need replacement and proactively order them.
Instead of scrambling to find the right part during an emergency, you have it on hand, ready for when the time comes. This strategy ensures that downtime is minimized and equipment is back up and running as quickly as possible.
Having an integrated supply chain means your inventory management system is connected to your usage data. When a part’s condition is nearing the end of its lifespan, the system automatically signals for replenishment.
Efficiency is soon seen across all maintenance activities, as maintenance teams are always prepared. Proactive parts management, coupled with real-time data, allows you to act faster, reduce waiting times, and avoid disruptions in production.
11. Employee Training Based on Equipment Usage Insights
In usage-based maintenance, the key is not just the equipment itself but also the people managing it. By analyzing equipment usage data, you can tailor training programs to address the specific needs of the operators.
If certain machines are used more intensively or in more complex conditions, operators can be trained to recognize signs of wear or issues specific to those conditions. This equips the team to act faster, before small problems become bigger ones.
Training becomes more effective when it’s informed by real-world data. Instead of focusing on broad maintenance tips, it hones in on the specific equipment and its usage profile.
Operators gain the necessary skills to deliver maintenance services, which increases the overall effectiveness of the maintenance strategy.
Implement FieldCircle CMMS to Optimize Your Usage-based Maintenance Strategy
Apart from other preventative maintenance strategies like time-based maintenance and condition-based maintenance, usage-based maintenance has its own relevance, which we looked at. To streamline its implementation all you need is a good maintenance software application.
FieldCircle’s maintenance management software makes usage-based maintenance more effective and manageable. By offering real-time data and detailed insights, it allows businesses to monitor actual equipment usage and pinpoint when maintenance is truly necessary.
With integrated sensors and predictive tools, FieldCircle helps maintenance teams take action quickly, preventing problems before they escalate. Our maintenance management system software brings all maintenance tasks together in one place, giving a comprehensive view of equipment health. Talk to our experts to start implementing the one-stop solution for your maintenance needs.