Top 10 Benefits of Predictive Maintenance
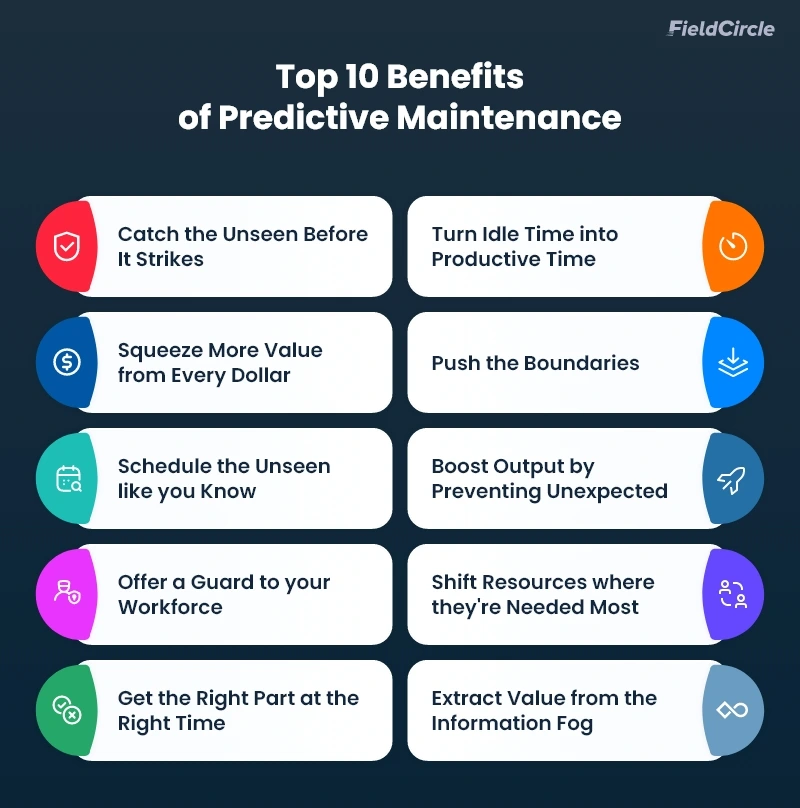
Businesses that still operate with a reactive approach to maintenance where they fix equipment only when something goes wrong incur several costs, both time and money. As a result, informed businesses are moving toward predictive maintenance to smartly drive their maintenance functions.
Predictive maintenance is emerging as a game-changer due to the myriad benefits it offers. From them, the following are the top 10 benefits of predictive maintenance that we will discuss in this blog.
- Catch the Unseen Before It Strikes
- Turn Idle Time into Productive Time
- Squeeze More Value from Every Dollar
- Push the Boundaries
- Schedule the Unseen like you Know
- Boost Output by Preventing the Unexpected
- Offer a Guard to your Workforce
- Shift Resources where they’re Needed Most
- Get the Right Part at the Right Time
- Extract Value from the Information Fog
1. Catch the Unseen Before It Strikes
Predictive maintenance integrates IoT-based sensors that monitor and measure real-time data like vibration, temperature, pressure, and humidity to analyze equipment and infrastructure usage and performance to detect early signs of equipment failure.
This approach analyzes critical data points using advanced analytics tools, such as condition monitoring, anomaly detection, ML platforms, infrared analysis, and AP predictive analytics. Such analysis – especially through a CMMS – helps maintenance teams receive early warnings to detect irregularities, receive alerts, and address issues before they transform into costly malfunctions.
Early fault detection allows businesses to avoid minor and catastrophic failures and improve overall operational stability. Implementing predictive maintenance in the manufacturing sector helped achieve a predictive accuracy of 90% and reduced potential downtime by 20% by identifying equipment failures early. Maintenance teams can perform target interventions instead of routine inspections based on real-time data, which translates to increased productivity and reliability.
Industries like aerospace and automotive that rely on complex equipment benefit significantly from early fault detection. For instance, aircraft with sensors constantly monitor different engine components, looking for stress and irregularities. Detecting issues early helps enhance operational safety while reducing unplanned breakdowns, allowing them to save millions in repairs and downtime costs.
2. Turn Idle Time into Productive Time
Unplanned equipment down halts the production line and cripples the entire business operations, especially in production-heavy industries. Utilizing predictive maintenance allows businesses to track equipment performance and health continuously, minimize such disruptions, and continue operations.
Analyzing real-time data based on sensor information helps companies predict and prevent equipment breakdowns. It allows businesses to service their machinery on time by scheduling maintenance activities during low-productivity hours instead of peak production time.
For example, a fleet management company analyzed real-time data from sensors and logs to monitor vehicle health, predict potential failures, and intervene on time, resulting in a 70% reduction in breakdowns and a 30-50% decrease in downtime.
Likewise, predictive maintenance becomes a bigger asset for sectors like manufacturing, where a few hours of downtime can lead to significant financial implications, missed deadlines, and damaged reputation. Predictive systems play a stabilizing role in preventing sudden stoppages, improving production timelines, and reducing idle labor and halted supply chain costs.
3. Squeeze More Value from Every Dollar
Unforeseen equipment failures result in costly repairs, productivity losses, increased operational costs, strained financial resources, disrupted production schedules, and resource mismanagement. Such breakdowns lead to immediate repairs, which cost more than planned maintenance.
Predictive maintenance solves these challenges by allowing companies to fix equipment before it requires emergency intervention. This proactive approach focuses on data-driven scheduling, allowing companies to allocate resources better, reduce labor waste, and improve long-term ROI.
For example, after implementing predictive maintenance, an oil refinery reduced maintenance costs by 20% and decreased emergency repair costs from $10 million annually to $8 million, with long-term savings projected at over $5 million.
Predictive maintenance also optimizes labor utilization by preventing equipment over-servicing. In logistics, companies track fleet health data to reduce unnecessary repairs and improve uptime and cost efficiency. By reducing downtime, enhancing fleet uptime, and boosting cost efficiency, companies can allocate the maintenance budget to strategic fleet improvements and long-term growth instead of reactive fixes.
4. Push the Boundaries
Proactive maintenance through predictive approach helps monitor wear and tear using sensors to detect early signs of degradation and replace parts before they fail. Early intervention reduces stress on critical parts that could cause cascading failure, shortening asset life and increasing repair costs. Fixing minor issues early avoids major breakdowns and repairs.
Studies show that projects using predictive maintenance save downtime by 35–50%, increase asset lifespan by 20–40%, decrease expenses, increase safety, and improve product quality. They can defer major equipment replacements and preserve capital for other strategic investments. For example, power generation facilities using predictive systems to monitor turbine performance successfully delay major capital expenditures for years, saving millions.
Predictive maintenance also improves reliability and operational efficiency so the equipment runs at peak performance. In industries like construction, where equipment downtime halts entire projects, it minimizes wear-related failures and costly delays. Extending the equipment life of cranes and excavators improves project quality, reduces disruptions, and creates safer job sites by preventing equipment failures that could cause accidents.
5. Schedule the Unseen like you Know
Predictive maintenance shifts the paradigm from fixed time-based maintenance schedules to a more flexible condition-based system. It uses real-time data and advanced analytics to determine the optimal time for maintenance tasks based on the equipment’s condition, minimizing equipment failure risk.
A study on predictive maintenance using machine learning and IoT showed a 20–30% decrease in maintenance expenses and a 30–40% decrease in unplanned downtime, suggesting more effective maintenance scheduling. By monitoring equipment performance indicators like temperature, vibration, or wear, maintenance teams better plan interventions. This reduces unnecessary maintenance, increases asset uptime, and allows for better resource allocation, so maintenance resources are focused on the most critical tasks.
Industries like chemical processing particularly benefit from this shift, with predictive maintenance reducing redundant tasks and improving safety compliance. Maintenance windows align with production schedules so operations run smoothly without unnecessary stops. Such alignment optimizes productivity and resource management, helping companies achieve considerable cost savings.
6. Boost Output by Preventing the Unexpected
Predictive maintenance keeps your equipment running at peak performance. By continuously monitoring performance metrics like energy consumption, output speed, and operational temperature, predictive systems help detect early signs of inefficiency or mechanical issues that hamper productivity. Addressing these issues early reduces energy waste, prevents delays, and maximizes equipment effectiveness.
For example, healthcare facilities use energy monitoring systems (EMS) to track HVAC, lighting, and other critical infrastructure. These systems, using AI-driven algorithms, improve energy efficiency by 36%, resulting in lower operational costs and a reduced carbon footprint. The same results are seen in manufacturing, where predictive maintenance ensures machines run at their best, with no performance deterioration and downtime.
Businesses using predictive maintenance experience more production output, especially in high-demand automotive and electronics manufacturing industries. Predictive systems help companies stay ahead by ensuring the optimal performance of machines at maximum capacity, reducing the need for unplanned repairs, and minimizing operational disruptions.
7. Offer a Guard to your Workforce
Predictive maintenance keeps your workplace safe by detecting potential hazards before they escalate. By monitoring temperature, pressure, and vibration, predictive systems identify early signs of equipment failure, allowing the maintenance team to intervene before dangerous situations like overheating or mechanical instability occur.
The manufacturing industry that adopts machine learning techniques improves its failure prediction accuracy by 25%, reducing the chances of equipment failure. Early detection means the machine operates within safe parameters, minimizing risk to people and the environment and meeting safety regulations.
Proactive maintenance is critical in high-risk industries like chemical processing and mining to prevent catastrophic failure. Continuous equipment monitoring avoids pressure build-up, hazardous leaks, and other critical failures, reducing the risk of fatal accidents and protecting surrounding communities.
Similarly, predictive maintenance strengthens the safety protocols with real-time equipment performance data. It allows safety managers to make informed decisions on inspections and part replacements and maintain high safety standards without downtime, creating a safety-first culture within the organization.
8. Shift Resources where they’re Needed Most
Predictive maintenance focuses on tasks based on urgency and criticality. Instead of fixed schedules, maintenance teams make data-driven decisions regarding maintenance. They prioritize time and resources based on real-time equipment health, helping remove unnecessary inspections and duplicate tasks.
Only performing maintenance when data indicates a risk of failure allows technicians to focus on higher-priority repairs and upgrades. It leads to reduced idle time and improved labor efficiency and equipment performance.
Predictive maintenance also improves inventory and material management. Knowing which parts will fail beforehand helps companies avoid overstocking, reduce inventory costs, and ensure the availability of critical parts when needed. Such an approach simplifies budgeting, reduces waste, and improves project timelines.
Following predictive maintenance improves workforce scheduling and operational flexibility. By optimizing repair timing, businesses align labor availability with production schedules, reduce delays, and improve project execution. This leads to smoother operations and a more agile workforce to meet changing demand.
9. Get the Right Part at the Right Time
Accurate forecasting of spare parts is key to equipment availability and uptime. Predictive maintenance uses analytics to track and predict component failures so businesses can optimize spare parts inventory. It gives continuous insights on the performance through various maintenance metrics. In a way, through these measures, businesses minimize the risk of overstocking, and so the capital is no more tied up and there are no shortages to stop production.
A McKinsey study found that companies that use AI in inventory management have 30% better part availability and 20% lower holding costs. In industries like mining, where long lead times disrupt operations, predictive maintenance alerts procurement teams in advance so they coordinate with suppliers and receive timely deliveries. In return, it reduces downtime and keeps costs under control.
By minimizing excess inventory and improving part readiness, businesses reduce storage costs, improve cash flow, and allocate capital more effectively. Predictive maintenance ensures critical parts are available when needed without the hassle of surplus stock.
Predictive systems also identify slow-moving or obsolete parts, preventing unnecessary purchases and directing attention toward frequently used components. Such an approach optimizes inventory levels, reduces waste, and makes better purchasing decisions.
10. Extract Value from the Information Fog
Predictive maintenance offers real-time insight into equipment performance for continuous improvement in asset management. Advanced analytics allows businesses to identify recurring issues, schedule maintenance, and make informed decisions about machinery upgrades and replacements. A data-driven approach increases operational reliability, reduces unexpected downtime and maximises equipment life.
For example, an auto manufacturer accurately detected 97% of defects using AI-powered visual inspection systems. By fixing defects early in production, predictive insights reduce rework and improve product quality. Such results show how predictive maintenance supports broader business goals like quality control, process optimization, and cost savings. With continuous monitoring, you can anticipate issues and take proactive action to improve operational efficiency.
In telecommunications, predictive data drives proactive network optimisation, reducing service disruptions and improving customer satisfaction. Telcos use real-time performance data to detect infrastructure issues before they impact customers, minimising downtime and improving service delivery.
Also, predictive maintenance creates a culture of continuous improvement across departments. Production managers can optimize workflows, while maintenance teams can refine repair strategies. With a proactive data-driven approach, companies mitigate risks, improve performance and make more profit.
Choose FieldCircle for Predictive Maintenance
Predictive maintenance enables businesses to improve efficiency, cut costs, and extend equipment life by fixing problems before they escalate.
With the help of predictive maintenance software, companies harness real-time data and implement proactive interventions to reduce downtime, optimize resource allocation, and ensure smooth operations.
Our tool improves productivity and provides a competitive edge by maintaining performance, improving safety, and reducing unexpected repairs. For companies looking to simplify and future-proof, our predictive maintenance is a vital strategic solution.