Preventive Maintenance Inspections: Meaning, Implementation, Checklist, and More
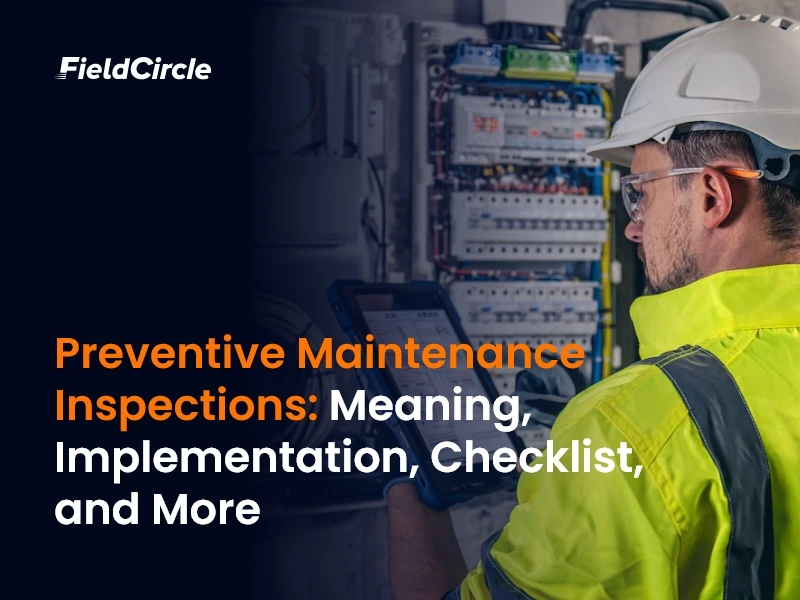
Inspections are a very important part of the preventive maintenance process. During the maintenance operations, the maintenance staff can carry out inspections for many reasons. These can be part of a predefined maintenance schedule, triggered by signs of improper machinery functioning, or recommended by stakeholders associated with specific equipment.
Monitoring the condition of equipment in the form of inspection keeps them in the best condition and it continues to work seamlessly. Inspections thus aim to minimize the disruptions and thus maintain the operational continuity while keeping costly repairs at the bay.
Inspections taken to prevent roadblocks or potential failures in operations by continuous monitoring of the equipment function render the maintenance process the “preventive” character, and they become part of a preventive maintenance strategy.
As we move ahead, we will offer you deep insights about preventive maintenance inspections discussing its meaning, the process to implement it, its elements and benefits, the maintenance checklist to have, and the best practices to follow. Keep reading.
What is Preventive Maintenance Inspection?
Preventive maintenance inspection is a careful examination of each and every element in the ongoing maintenance operations to ascertain if processes are working ideally. They evaluate the current state of equipment or systems without necessarily fixing anything right then and there but emerges with insights that aid in and drive maintenance.
Key elements of PMI include:
- Inspection Checklists: Tailored to specific equipment, ensuring all critical components are assessed.
- Condition-Based Monitoring: Utilizing sensors, thermal imaging, vibration analysis, and other techniques to detect early signs of wear or malfunction.
- Compliance & Safety Verification: Ensuring adherence to industry standards and regulatory requirements to prevent safety hazards.
- Lubrication & Calibration: Routine servicing of moving parts and recalibrating instruments to maintain efficiency to lubricate machinery and ensure optimal performance.
- Historical Data Analysis: Leveraging maintenance logs and performance metrics to refine inspection schedules and predict failures.
What is the Process to Implement Preventive Inspection?
Implementing a preventative maintenance inspection process requires a systematic approach to assess the existing maintenance framework. Each step must be executed with precision as the following explanation shows:
-
Evaluate the Existing Maintenance Framework
Assess the current maintenance setup by identifying whether the approach is reactive or preventive. Review which assets receive regular inspections and which do not. This analysis provides insight into areas requiring optimization, helping identify gaps in resources or processes that need improvement to create a solid foundation for the preventive maintenance program.
-
Define the Objectives of the Preventive Maintenance Program
Set clear, measurable objectives for the preventive maintenance program. Focus on minimizing unscheduled downtime, optimizing asset lifespan, boosting safety standards, and lowering long-term maintenance costs. These goals direct the entire maintenance strategy, keeping it aligned with both technical and business needs and ensuring more efficient operations over time. They are important from productivity and cost savings perspectives.
-
Categorize and Prioritize Assets
Organize assets into categories based on importance and urgency. Start by creating an asset inventory with essential details like manufacturer specifications, current condition, and maintenance history. Assess the criticality and potential risks each asset poses to operations. Prioritize inspections based on these factors to allocate resources effectively and avoid unnecessary work on less significant assets.
-
Create a Preventive Maintenance Plan
Develop a detailed preventive maintenance plan with specific actions, schedules, and tasks for each asset. Define inspection intervals based on manufacturer recommendations or usage data. Outline tasks such as cleaning, lubrication, or more technical checks. Ensure all inspections meet industry standards, document findings, and track any abnormalities to provide a complete record for future reference.
-
Select and Implement a Maintenance Management System (CMMS)
Choose a CMMS that supports key functions such as asset tracking, work order management, and inspection scheduling. Select one that integrates with other systems, including ERP and inventory management. A well-chosen CMMS helps automate maintenance tasks, track progress, and store historical data, giving teams an organized system to monitor and improve maintenance activities.
-
Train and Equip Maintenance Personnel
Offer ongoing training to maintenance teams on procedures, tools, and technology, such as diagnostic equipment and CMMS. Conduct regular preventive maintenance training on safety protocols and proper handling of equipment promotes the team’s competence and adherence to regulations, ensuring inspections meet organizational standards.
-
Schedule and Execute Preventive Maintenance Inspections
Implement automated scheduling within the CMMS to assign tasks, set inspection intervals, and track progress. Inspections are scheduled based on predefined criteria, and technicians follow the outlined maintenance tasks and document findings during inspections. Timely execution and accurate reporting ensure that maintenance goals are met, and no tasks are skipped, preventing potential equipment failures or missed issues.
-
Analyze and Interpret Inspection Results
Examine data from inspections to detect patterns and emerging issues. Identify frequent failures across similar assets to spot potential design flaws or weak components. By analyzing failure patterns, teams can refine their inspection protocols and maintenance strategies. Reactive maintenance strategies can be avoided by addressing minor issues before they turn into major, costly repairs.
-
Take Corrective Actions Based on Findings
Address issues found during inspections with prompt corrective actions. Prioritize repairs based on urgency, planning downtime efficiently to minimize operational disruptions. Technicians document repairs and track their success, ensuring that recurring problems are addressed thoroughly. Identifying root causes helps rectify further failures and optimizes asset longevity.
-
Leverage Technology to Optimize Preventive Maintenance
Apart from CMMS, use technologies like IoT sensors and robotics to elevate preventive maintenance efforts. Sensors provide real-time data on equipment conditions, while robotics assist with inspecting hard-to-reach areas, offering efficiency and reducing human error. As integral operational components, these technologies make effective preventive maintenance easier and more accurate.
What Should Be Included in a Preventive Maintenance Inspection?
PM Inspections should include visual inspections, electrical system checks, performance testing, lubrication, fluid level monitoring, and safety feature verification to ensure that all critical equipment aspects are reliable, efficient, and safe. These inspections are vital to maintain machinery and equipment in optimal condition while minimizing the risk of unexpected failures.
-
Visual Inspections
It includes checking equipment for visible signs of wear, corrosion, or damage that could affect functionality. All connections, bolts, and fasteners should be inspected for looseness, and any leaks or cracks should be identified early to prevent further deterioration. Also, verify that safety labels and instructions are legible and intact to ensure usage and compliance.
-
Electrical System Inspection
During an electrical system inspection, maintenance teams should examine all wiring, connections, and electrical components for fraying, corrosion, or looseness. Testing voltage levels and load capacity are essential to prevent electrical failures. It is also necessary to verify the proper working of circuits, breakers, fuses, and protective relays to reduce electrical hazards.
-
Performance Testing
Testing equipment performance under normal conditions to assess its efficiency, stability, and overall functionality helps identify and address unusual noises, excessive vibrations, and overheating issues. Performance testing also includes checking the alignment and calibration of moving parts and load testing to ensure operational accuracy.
-
Lubrication and Cleaning
Proper lubrication and cleaning of moving parts, according to the manufacturer’s recommendations, help minimize friction and wear. It is essential to clean dust, dirt, and debris regularly to prevent clogging and overheating of critical components. Air filters, heat exchangers, radiators, and cooling systems should also be cleaned and replaced periodically to maintain airflow efficiency.
-
Fluid Level Checks
Monitoring and maintaining the optimal level of oil, coolant, and hydraulic fluid is an essential part of preventive maintenance. It is crucial to detect fluid leaks from seals, reservoirs, or lines to prevent failures and maintain continuous operations. Additionally, fluid quality should be tested and replaced (if necessary) to ensure the proper operation of the fuel systems.
-
Safety Feature Checks
Examining safety features allows organizations to prevent accidents and maintain regulatory compliance. This includes checking the functionality and working condition of emergency stop buttons, alarms, protective systems, smoke and carbon monoxide detectors, and fire suppression systems (e.g., fire extinguishers). Organizations should also have personal protective equipment (PPE) readily available to maintain workplace safety.
What are the Benefits of Preventive Maintenance Inspections?
A systematic examination and assessment of components, systems, or machines, through visual checks, measurements, or diagnostic tools, to detect signs of wear or malfunction is carried out in preventive maintenance inspections. This is what makes inspections important in the overall maintenance. Right from bolstering the reliability of the equipment, the process helps in numerous ways such as:
-
Systematic Identification of Degradation
Inspections are designed to methodically identify early signs of component degradation, such as cracks, corrosion, or unusual wear patterns. This allows for precise identification of parts that may require attention, ensuring targeted repairs and reducing the likelihood of unnoticed failures.
-
Verification of Operational Performance
Inspections validate that systems are operating within their designed parameters. For instance, checking pressure levels in hydraulic systems or the temperature in electrical circuits ensures components perform at their optimal efficiency. This verification process prevents system inefficiencies that could lead to unnecessary energy consumption or diminished output.
-
Timely Identification of Systematic Issues
Inspections allow for a thorough examination of interconnected systems, helping detect issues that might affect multiple components. For example, misalignment in mechanical parts may lead to system-wide failures. Identifying such problems early can prevent a cascading effect of breakdowns in the entire system.
-
Accurate Documentation for Maintenance History
Through regular inspections, you evaluate the condition of equipment and capture it in a detailed log. This documentation can be used for tracking the health of assets over time, identifying recurring issues, and supporting data-driven decisions on when to replace parts, all of which are critical for long-term maintenance strategies.
-
Prevention of Unscheduled Downtime
Regular checks on motors, pipes and other critical parts prevent the development of major repair issues that might lead to long-term downtime. For instance, examining fluid levels, checking electrical connections, and verifying structural integrity can highlight problems that might have led to equipment failure, thus avoiding sudden interruptions in service.
-
Support for Predictive Maintenance Strategies
Inspections provide a critical data point for implementing predictive maintenance. By collecting and analyzing condition data (e.g., vibration, temperature, or pressure readings), businesses can predict potential failures, allowing for more accurate scheduling of maintenance repairs or replacements based on actual system performance rather than generalized timelines.
-
Remain Compliant with Lease and Legal Requirements
For landlords managing commercial properties, inspections become part of the lease agreement, where maintaining systems like plumbing, HVAC, electrical components, and even roofs and ceilings is crucial. Inspections ensure compliance with building codes and prevent legal disputes related to system malfunctions that could affect tenants.
Checklist For Preventive Maintenance Inspection
Following is a maintenance checklist for maintenance inspection which you can tailor based on the specific equipment or systems you’re inspecting.
Equipment Overview
- Make, Model, and Serial Number: Verify equipment details and confirm they match records.
- Location: Ensure the equipment is in the correct, designated location.
- Operating Hours: Record and verify operating hours since the last inspection.
Physical Condition
- Signs of Wear and Tear: Look for cracks, dents, rust, or corrosion. Leaks: Check for any fluid or gas leaks around machinery, pumps, valves, etc.
- Cleaning: Assess cleanliness; ensure no dust, debris, or build-up that could affect operation.
- Vibration or Noise: Listen for unusual sounds or vibrations, indicating mechanical issues.
Functional Checks
- Startup and Shutdown: Test the equipment’s startup and shutdown procedures to ensure smooth operation.
- Operational Test: Run the equipment or system to check for any abnormalities in performance (e.g., speed, pressure, temperature).
- Controls and Indicators: Test all control systems, gauges, lights, and indicators to ensure they are functioning properly.
- Safety Mechanisms: Verify that all safety switches, alarms, and shutdown features are working as intended.
Electrical Components
- Power Supply: Ensure the electrical connections are stable, and check for signs of overheating.
- Wiring and Connections: Inspect for frayed wires, loose connections, or exposed conductors.
- Grounding: Confirm that grounding is correct and secure.
- Battery (if applicable): Check charge levels, clean terminals, and inspect for any leakage or damage.
Mechanical Components
- Belts and Chains: Inspect for wear, cracks, or elongation; ensure proper tension.
- Bearings and Bushings: Check for lubrication levels and signs of wear or damage.
- Couplings and Housings: Examine for cracks, misalignment, or excessive movement.
- Hydraulic and Pneumatic Systems: Test pressure levels and check hoses for leaks or signs of damage.
Lubrication
- Lubricant Levels: Check oil, grease, and other lubricants; top off or replace as needed.
- Lubrication System: Inspect the system for blockages, leaks, or signs of wear.
- Lubricant Quality: Ensure that the lubricant is free of contaminants, dirt, or metal shavings.
Cooling and Heating Systems
- Heat Exchangers and Fans: Check for proper operation, cleanliness, and airflow.
- Cooling System: Ensure coolant levels are adequate and verify there are no leaks in hoses or radiators.
- Filters and Screens: Inspect air filters, strainers, and other filtration systems for blockages or wear.
Environmental Conditions
- Temperature and Humidity: Verify that environmental factors (temperature, humidity) are within acceptable operating ranges.
- Ventilation: Check for proper airflow and ventilation in rooms housing critical equipment.
- Noise Levels: Measure and assess any excess noise that could signal malfunctioning parts.
Safety Equipment
- Personal Protective Equipment (PPE): Ensure that necessary PPE (guards, barriers, warning labels, etc.) is intact and accessible.
- Fire Extinguishers and Emergency Equipment: Verify placement, inspection dates, and functionality.
- Lockout/Tagout Procedures: Check that lockout/tagout procedures are up to date and accessible.
Best Practices for Implementing Preventive Maintenance Inspections
Following are the best practices that are not theoretical but are widely used across industries such as manufacturing, energy, transportation, and healthcare. Adhere to these best practices for the best outcome from your preventive maintenance inspections.
Follow a Standardized Inspection Procedure
- Use predefined checklists specific to the equipment or system being inspected.
- Follow manufacturer-recommended inspection intervals and procedures.
- Use a clear pass/fail or condition grading system (e.g., “Good,” “Needs Attention,” “Critical”).
Maintain Accurate and Detailed Records
- Record inspection results digitally in a computerized maintenance management system (CMMS) or inspection logbook.
- Include time-stamped photos of defects or wear and tear for future comparison.
- Track equipment history to identify recurring issues and trends.
Schedule Inspections Based on Operational Data
- Align inspections with equipment operating hours rather than arbitrary calendar dates.
- Use sensor-based monitoring (e.g., vibration analysis, thermal imaging, oil analysis) to determine inspection timing.
- Adjust schedules dynamically based on past failure patterns and predictive analytics.
Use Qualified and Trained Inspectors
- Assign inspections only to certified technicians or personnel trained in the specific equipment.
- Provide ongoing training on regulatory compliance, safety protocols, and emerging diagnostic tools.
- Conduct periodic audits to validate the accuracy and consistency of inspections.
Adhere to Safety Protocols
- Follow Lockout/Tagout (LOTO) procedures before inspecting electrical or mechanical systems.
- Use personal protective equipment (PPE) relevant to the equipment (e.g., gloves, safety glasses, arc flash protection).
- Verify that fire suppression, emergency stops, and safety interlocks are functioning before beginning inspections.
Utilize the Right Inspection Tools and Technology
- Use thermal imaging cameras to detect overheating components.
- Apply ultrasonic testers for early-stage bearing failures.
- Leverage oil analysis for hydraulic and lubrication system condition assessment.
- Implement IoT-based condition monitoring sensors for real-time performance tracking.
Prioritize and Act on Inspection Findings
- Categorize issues based on severity (e.g., immediate action, scheduled maintenance, monitor for change).
- Establish a response timeframe for different defect levels (e.g., critical failures require same-day intervention).
- Flag recurring failures for further root cause analysis.
Ensure Proper Documentation and Compliance
- Align inspections with OSHA, ISO 55000, NFPA, or other industry-specific standards.
- Maintain detailed audit trails for regulatory and insurance purposes.
- Store inspection reports centrally to allow for trend analysis and informed decision-making.
Incorporate Predictive Maintenance Insights
- Use historical failure data to refine inspection criteria and adjust schedules.
- Monitor vibration analysis, thermal performance, and real-time sensor data to detect anomalies before failures occur.
- Integrate AI-driven maintenance analytics to predict potential breakdowns based on past inspections.
Continuously Improve Inspection Processes
- Conduct post-inspection reviews to refine procedures and update checklists.
- Gather feedback from technicians on inspection challenges and required process adjustments.
- Benchmark against industry best practices to adopt new and more effective inspection methods.
Let FieldCircle aid you Implement Inspections
Maintenance is critical and inspections as part of this critical process require you to have the right tools to best perform inspection procedures.
FieldCircle’s preventive maintenance software takes the hassle out of inspections by turning paper checklists into digital ones. Inspectors can easily access them on mobile devices, log data, and upload photos on the spot, cutting down on errors and speeding up the whole process. Our one of a kind maintenance tool automatically schedules tasks, so nothing gets overlooked, and keeps everything in one place for easy access and tracking.
With all the data stored and ready to go, teams can quickly spot recurring issues and trends. Further, real-time data capture and automatic scheduling make inspections quicker, more organized, and less prone to mistakes. Drop a line to know how FieldCircle makes performing preventive maintenance inspections a lot easier.