Role of Condition-based and Preventive Maintenance in Reliability-centered Maintenance
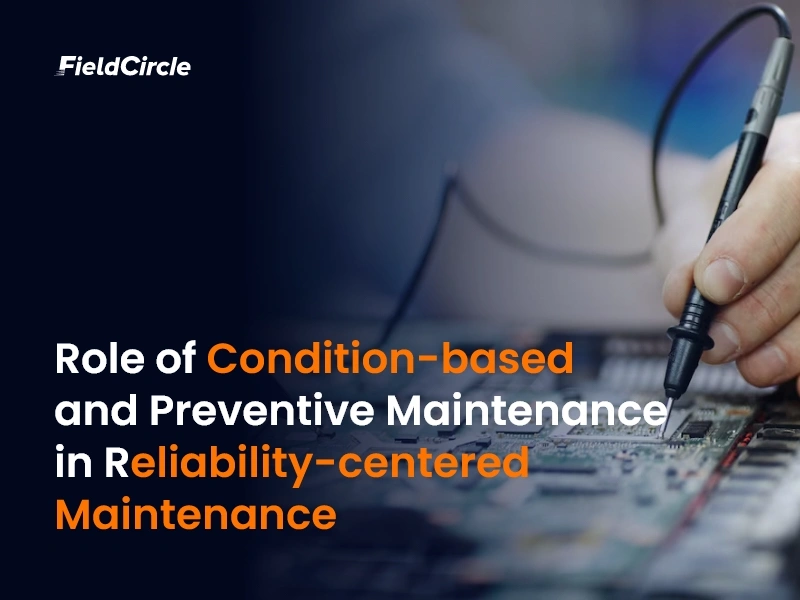
The greatest risk to asset reliability is not equipment failure, but a maintenance strategy that fails to anticipate it.
Maintenance managers often find themselves caught in a reactive cycle, which strains resources and hampers overall productivity. What is left is a little room for strategic planning, which results in inefficiencies and heightened costs.
Should maintenance managers prioritize preventive maintenance (PM) to reduce the risk of equipment failure, or should they choose condition-based maintenance (CBM) to monitor equipment health in real-time?
Over-investing in PM or neglecting CBM can lead to unnecessary failures, ultimately costing more than just money—it can also impact reliability, productivity, and overall asset management. They need to carefully analyze how each of these two types of maintenance strategies is going to aid them in implementing the RCM program.
By combining condition-based maintenance (CBM) with preventive maintenance (PM), businesses can establish a reliable and cost-effective maintenance program that minimizes downtime and extends the life cycle of critical equipment.
These strategies are essential within Reliability-centered maintenance (RCM) and facilitate a shift from reactive maintenance to proactive maintenance, thereby improving overall reliability and efficiency. We see how each of them plays an important role in reliability-centered maintenance.
What is Reliability-Centered Maintenance (RCM)?
Reliability-centered maintenance (RCM) is a maintenance approach that focuses on identifying the most effective maintenance actions for assets by evaluating their functions, failure modes, and the impact of failures. It aims to optimize maintenance efforts, reduce downtime, and manage maintenance costs by aligning actions with actual system needs and risks.
Using RCM, companies can identify the maintenance tasks that are most critical for each piece of equipment. This way, RCM helps classify the levels of maintenance required, focusing attention on the most essential components.
The main difference between RCM and traditional maintenance approaches lies in its proactive nature. Instead of reacting to failures, RCM encourages preemptive actions, such as predictive maintenance (PdM), which significantly reduces the probability of failure and ensures that assets are maintained in a way that aligns with their operational importance.
As a type of proactive maintenance, RCM improves overall equipment effectiveness (OEE) by ensuring that assets always operate at peak performance, reducing the frequency and duration of downtime. According to a report from McKinsey & Company, companies that implement RCM see an 18-25% reduction in maintenance costs and a 5-15% increase in asset availability.
What is the Role of Preventive Maintenance (PM) in RCM?
Preventive maintenance complements the principles of RCM by ensuring that the maintenance efforts are focused on the right equipment, based on their importance to the operation, and geared toward preventing the most impactful failures. It supports RCM through
-
Execution through Scheduled Intervals
Preventive maintenance helps maintain RCM’s structured approach by implementing the required actions at defined intervals. These intervals are set based on the findings from RCM analysis, making sure that equipment receives the right attention at the right times, without delays, thus reducing the risk of failure due to missed maintenance.
-
Systematic Elimination of Potential Failure Causes
Preventive maintenance focuses on removing the root causes of failure identified in the RCM analysis. It addresses recurring issues—such as mechanical wear or contamination—that, if left unchecked, lead to system malfunctions. Regular replacement or servicing of vulnerable components prevents a build-up of failures over time, which reduces the number of unplanned downtime.
-
Refinement of Failure Mode and Effect Analysis (FMEA)
As preventive maintenance is carried out, it provides real-time data on equipment performance. The data helps to refine the failure modes in the FMEA, adjusting failure probabilities and consequences. By performing routine maintenance checks, teams gather insights into how components behave, which feeds directly back into RCM’s proactive strategy of focusing on failure prevention rather than just repair.
-
Strategy Adjustment Based on Historical Data
Through ongoing preventive maintenance, the performance history of equipment is continuously recorded. The historical data allows for a better understanding of when and why failures occurred in the past, and aids in the adjustment of maintenance strategies. The patterns obtained guide more accurate decision-making about when to implement more targeted interventions or shift maintenance approaches.
-
Mitigation of Unpredictable Asset Failures
In RCM, the focus is placed on minimizing unpredicted breakdowns, which can bring operations to a halt. Preventive maintenance works by addressing small, early signs of wear and helps avoid costly failures. By catching these issues early, maintenance teams help stop problems before they escalate into emergency maintenance, which would disrupt operations and incur higher repair costs.
-
Optimized Allocation of Resources
Preventive maintenance aligns with RCM’s goal of using resources efficiently by focusing efforts on the most significant aspects of maintenance. Scheduled maintenance through timely checks, part replacements, and diagnostics is performed in a way that spreads resources optimally across critical assets, which avoids wasteful over-maintenance of low-priority equipment and directing efforts where they are most needed.
What is the Role of Condition-Based Maintenance (CBM) in RCM?
As a maintenance approach, condition-based maintenance(CBM) provides real-time insights into equipment health, helping maintenance teams make data-driven decisions based on the actual performance of assets. It aids the RCM process by offering:
-
Immediate Response to Performance Shifts
CBM tracks key parameters like temperature, vibration, and pressure. When these parameters stray from expected levels, it triggers an alert. As a result, maintenance teams can jump on problems right away, thereby preventing small issues from snowballing into major breakdowns. If failure may occur due to these shifts, early detection prevents extensive damage.
-
Data-Driven Maintenance Focus
CBM shifts maintenance from fixed schedules to data-driven action. Maintenance happens when real data shows that an asset needs attention, rather than following arbitrary timelines. This way, teams spend their time fixing what matters most, rather than working off assumptions.
-
Early Warning for Potential Failures
By observing trends over time, CBM spots early signs of failure before they disrupt operations. Tracking these early indicators means maintenance teams tackle issues before they cause unexpected downtime, keeping systems running smoothly.
-
Flexible Maintenance Scheduling
With CBM, maintenance schedules adjust based on the real-time condition of assets. When a machine is running smoothly, maintenance efforts can be deferred, whereas a piece of equipment showing signs of trouble gets prioritized. The flexibility imparts the ability to make the best use of resources.
-
Continuous Monitoring for Ongoing Insights
The real-time nature of CBM provides a constant stream of data that keeps maintenance teams in the loop at all times. The ongoing feedback lets teams make quick decisions on repairs, alterations, or adjustments, without waiting for scheduled checks.
-
Cost Savings Through Targeted Maintenance
Rather than overhauling equipment on a fixed schedule, CBM targets interventions to areas where they are truly needed. By fixing only the components showing wear or malfunction, teams reduce unnecessary maintenance.
-
Integrating PM and CBM within RCM
Within the RCM framework, both PM and CBM play crucial roles, as we saw above. The choice between them—or the decision to use a combination of both—depends on various factors, including the criticality of equipment, failure modes, and operational contexts. There are two ways to integrate PM and CBM which are strategic integration and hybrid approach.
Strategic Integration is performed as follows:
- Critical Assets: For equipment whose failure could lead to significant safety hazards or maintenance and operational disruptions, integrating CBM allows for continuous monitoring and timely interventions, ensuring high reliability.
- Non-Critical Assets: For less critical equipment, PM might suffice, as the consequences of unexpected failures are manageable, and the costs of implementing CBM may not be justified.
The Hybrid Approach suits as discussed:
In many cases, a hybrid approach is adopted, where PM is performed at regular intervals, and CBM is used to monitor specific parameters that are critical to equipment performance. The combination ensures a balance between reliability and resource utilization.
Addressing the Key Challenges
Preventive maintenance and condition-based maintenance boost the efficiency of maintenance activities. However, following are the key challenges that stand in the way of maintenance teams optimize system reliability by combining Preventive Maintenance (PM) and Condition-Based Maintenance (CBM):
- Data management conflicts: Scheduled PM tasks and real-time CBM insights can sometimes conflict. To address this, many businesses adopt a computerized maintenance management system (CMMS) to centralize maintenance data, which aids in aligning maintenance activities.
- Balancing maintenance efforts: Excessive preventive tasks can waste resources, while relying solely on CBM may overlook critical issues. Prioritizing assets and refining maintenance strategies optimize efficiency.
- Skill limitations: CBM requires expertise in sensor data interpretation, which many teams lack. Regular training and cross-functional collaboration help close this gap.
- Conflicting maintenance schedules: Static PM routines may overlap with CBM recommendations, leading to redundant or missed interventions. Adjusting preventive maintenance plans based on real-time data ensures better coordination.
- Technology constraints: Many older systems lack the ability to handle advanced predictive maintenance or condition-based monitoring. Integrating unique maintenance tools like FieldCircle can help bridge these gaps and provide a seamless data exchange between PM and CBM systems.
- Uncertainty in predictive insights: Environmental changes and sensor inaccuracies can reduce forecasting reliability. Machine learning models and redundant monitoring improve prediction accuracy.
- Resistance to new approaches: Traditional teams may be reluctant to adopt data-driven maintenance methods. Gradual implementation, leadership support, and pilot programs help ease the transition.
Harness the Power of CBM and PM for RCM with FieldCircle
FieldCircle’s maintenance system integrates both condition-based maintenance and preventive maintenance seamlessly. It supports maintenance schedulers by providing real-time insights and aligning with RCM programs, thereby significantly boosting the overall maintenance strategy
The system provides all required maintenance checklists to ensure that work orders are scheduled on time, optimizing both time-based and condition-based maintenance activities. With its learning center, teams can continually refine their approach to maintenance, achieving the optimal maintenance balance for each piece of equipment.