What is Equipment Maintenance?
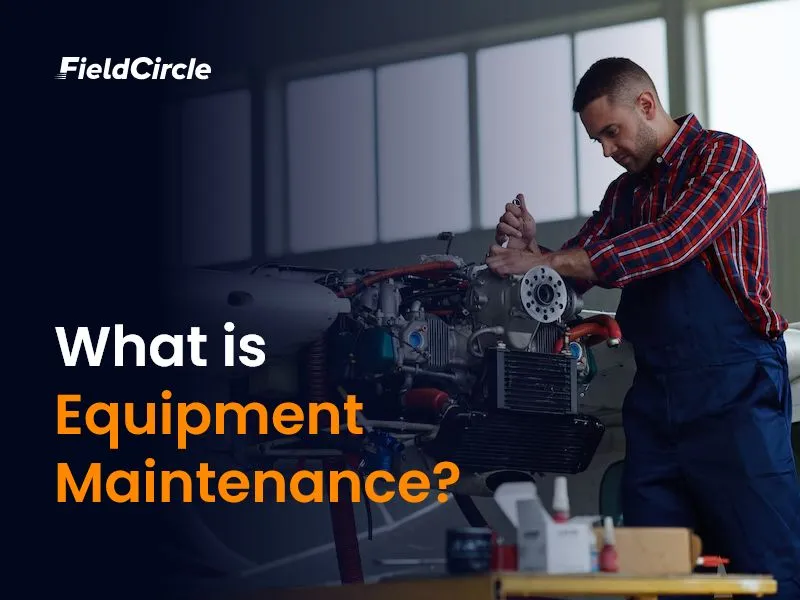
Equipment maintenance refers to a comprehensive range of routine activities aimed at preserving the functionality and longevity of machinery and equipment as well as preventing unexpected failures. These activities encompass inspection, cleaning, servicing, repairing, and replacing parts to ensure optimal working conditions. Equipment maintenance is crucial for preventing unexpected breakdowns and extending the lifespan of machinery, thus minimizing downtime and maximizing productivity.
Utilizing technology solutions, such as real-time tracking and maintenance logs, streamlines maintenance processes, enabling efficient scheduling and execution of tasks. Equipment maintenance teams play a vital role in planning, executing, and analyzing maintenance tasks effectively, ensuring equipment operates at its peak performance level.
As we move further in our discussion, we will cover the ins and outs of equipment maintenance to help you get the most out of your assets. Additionally, we will explore the importance of equipment maintenance, its types, industries, and certifications indispensable for your technical staff.
Importance of Equipment Maintenance
Equipment maintenance is important, as it serves as a preventive measure against unexpected breakdowns and malfunctions. By implementing regular maintenance routines, organizations can significantly reduce the risk of costly interruptions to operations and extend the overall lifespan of their machinery. This proactive approach not only minimizes downtime but also enhances productivity and operational efficiency, ultimately contributing to the organization’s ROI (Return on Investment).
Let us ask you a question: When was the last time you ensured that your business’s critical assets were effectively managed, monitored, and optimized? Even more importantly, do you have a roadmap or well-defined strategy to oversee your equipment?
If you are leading a facility, equipment management is pivotal for the seamless functioning and success of your business. Primarily because unexpected malfunctions or inefficiencies in your essential machinery can be detrimental to your growth, daily operations, and, ultimately, your financial stability.
This is where equipment management steps in: it encompasses a comprehensive approach to overseeing your assets, minimizing the potential of breakdowns, and maximizing performance, allowing you to focus on your core business activities. It encompasses a wide range of activities, including inspection, cleaning, servicing, repairing, and replacing parts, all aimed at preserving equipment in optimal working condition. By following practical equipment maintenance tips, businesses can streamline these processes and extend the lifespan of their machinery more effectively. Below, we have listed some reasons why it is important:
a. Prolongs Equipment Life – Regular maintenance prevents wear and tear, scheduling inspections and tasks to ensure longevity.
b. Prevents Unplanned Downtime – Maintenance minimizes unexpected breakdowns, utilizing real-time data to anticipate and mitigate potential failures.
c. Improves Efficiency and Performance – Maintenance optimizes equipment efficiency with analytics for performance tracking and optimization.
d. Enhances Safety – Maintenance supports a safe working environment, utilizing compliance checklists and logs to uphold safety standards.
e. Ensures Compliance with Regulations – Maintenance plays a crucial role in meeting industry regulations and maintaining accurate records for compliance.
f. Maintains Equipment Value – Maintenance preserves the resale value of equipment through detailed records and schedules.
Types of Equipment Maintenance
Understanding the various types of equipment maintenance strategies is crucial for optimizing asset performance and minimizing downtime. Below we have listed three types of equipment maintenance:
Reactive Maintenance
Reactive maintenance is a strategy where repairs are conducted only after equipment failure has occurred. Relying solely on reactive maintenance can result in increased maintenance costs and extended equipment downtime. However, businesses can transition from a reactive to a proactive maintenance approach, which involves tracking and analyzing failure patterns. This can help organizations reduce their reliance on reactive measures, thereby minimizing downtime and associated costs.
Preventive Maintenance
Preventive maintenance involves scheduled maintenance performed to prevent equipment from failing unexpectedly. This approach emphasizes the importance of routine equipment upkeep in reducing unforeseen breakdowns and prolonging equipment lifespan. It facilitates the scheduling, tracking, and documentation of maintenance activities, ensuring that all equipment receives timely attention. By adhering to a preventive maintenance schedule, your business can minimize breakdowns and optimize its equipment’s operational efficiency over time.
Predictive Maintenance
Predictive equipment maintenance is a data-driven approach that predicts equipment malfunctions before they occur. It relies on real-time data, analytics, and predictive algorithms to identify early signs of potential failures. Leveraging IoT sensors and machine learning technologies, predictive maintenance provides actionable insights that enable maintenance teams to address issues before they escalate into failures. This approach optimizes maintenance schedules and resource allocation, maximizing equipment uptime and performance while minimizing costs associated with reactive repairs.
Benefits of Using Equipment Maintenance
There are significant advantages of implementing a robust equipment maintenance strategy that benefits across various operational aspects. Following are some of its benefits:
I. Enhanced Operational Reliability – Consistent equipment maintenance leads to reliable operational processes, minimizing unexpected failures. Maintenance scheduling and real-time monitoring features contribute to enhancing operational reliability.
II. Cost Efficiency – A well-orchestrated maintenance plan brings cost-saving benefits, including reduced need for emergency repairs and lower long-term equipment costs. It aids in planning and executing cost-efficient maintenance strategies.
III. Safety Improvement – Regular maintenance ensures the safety of both equipment and its operators. Through checklists and maintenance records, it supports adherence to safety standards and protocols.
IV. Compliance with Industry Standards – Maintenance plays a crucial role in ensuring compliance with regulatory standards and avoiding penalties. It aids in compliance through detailed documentation and audit trails.
V. Increased Equipment Lifespan – Regular maintenance extends the usable life of equipment, preventing premature replacement. Predictive maintenance capabilities can forecast potential issues before they escalate.
VI. Improved Asset Management – Maintenance contributes to better asset management by keeping equipment in prime condition and ready for use. It offers asset management features that provide a comprehensive overview of all equipment statuses.
VII. Data-Driven Decisions – Data plays a crucial role in making informed maintenance decisions, from scheduling to resource allocation. It leverages data analytics to optimize maintenance activities.
VIII. Optimized Resource Allocation – Effective maintenance ensures optimal use of both human and material resources. It enables smart resource allocation to maximize efficiency and productivity.
Industries That Use Equipment Maintenance
Equipment maintenance ensures operational efficiency, safety, and compliance in a facility. It has a critical role across different sectors. Below, we have listed the industries that majorly uses equipment maintenance:
Manufacturing – The manufacturing industry heavily relies on heavy machinery and production lines. Preventive and predictive maintenance plays a crucial role in minimizing downtime and maintaining production schedules.
Construction – Maintaining equipment is essential in construction to ensure project timelines are met and safety standards are upheld. Scheduling maintenance and tracking equipment status are critical aspects of this industry.
Food and Beverage – Equipment maintenance is vital for hygiene, safety, and efficiency in food processing and production. Adhering to health regulations and managing maintenance schedules are priorities in this industry.
Hospitality – In the hospitality industry, maintenance impacts guest experience and operational efficiency, from kitchen equipment to HVAC systems.
HVAC—Regular maintenance is crucial for HVAC systems to operate efficiently, reduce energy costs, and improve air quality.
Mining – Equipment maintenance is paramount for safety and productivity in mining operations. Solutions like Field Circle assist in managing maintenance tasks and ensuring compliance with safety regulations.
Healthcare – Maintenance in healthcare is critical to ensure medical equipment functions accurately, affecting diagnoses and patient care.
Fleet – Maintaining fleet vehicles is crucial for reliability, safety, and operational efficiency. Optimizing fleet maintenance schedules is essential in this sector.
Oil and Gas – Equipment maintenance is critical for safety, environmental protection, and uninterrupted operations in the oil and gas industry. Predictive maintenance can help avert disasters.
Aerospace – Maintenance in the aerospace industry is crucial for safety, compliance, and performance. It supports rigorous maintenance protocols, ensuring regulatory compliance and aerospace safety.
Job Roles in Equipment Maintenance
Equipment maintenance and various key roles ensure the efficient operation, reliability, and longevity of machinery across industries.
Maintenance Technician
They are among the primary workers in the equipment maintenance sector who are responsible for the hands-on execution of maintenance tasks. Maintenance technicians’ primary tasks include inspecting, repairing, and performing routine maintenance on machinery and equipment. They play a critical role in ensuring the operational efficiency and reliability of equipment.
Their expertise and diligence in carrying out maintenance tasks directly impact the performance and longevity of machinery. With features such as mobile access and work order management, technicians can efficiently and effectively carry out their responsibilities, ensuring minimal downtime and optimal equipment performance.
Maintenance Supervisor
The Maintenance Supervisor holds a pivotal role in overseeing the maintenance team within an organization. They are responsible for prioritizing maintenance tasks, ensuring that maintenance schedules are adhered to, and coordinating maintenance efforts to ensure minimal downtime and optimal equipment performance. Maintenance Supervisors engage in strategic planning to identify areas for improvement and implement measures to enhance maintenance processes.
They utilize scheduling and analytics tools to facilitate these tasks, providing them with the oversight needed to make informed decisions. By effectively managing the maintenance team and resources, Maintenance Supervisors contribute significantly to maintaining operational efficiency and reliability across the organization.
Maintenance Manager
Maintenance Managers are responsible for developing, implementing, and evaluating maintenance strategies across the organization. They play a pivotal role in budgeting, resource allocation, and long-term maintenance planning to align with organizational goals. Maintenance Managers oversee the entire maintenance operation, ensuring that it operates smoothly and efficiently.
These people utilize comprehensive platforms that offer insights into maintenance operations, enabling them to optimize strategies and improve cost efficiency. By leveraging data and analytics, Maintenance Managers can identify trends, anticipate maintenance needs, and implement proactive measures to enhance equipment reliability and performance. In short, maintenance managers play a crucial role in ensuring the operational efficiency and reliability of equipment, thereby contributing to the organization’s success.
Equipment Maintenance Certifications
Following are some of the essential certifications that maintenance technicians should have:
Certified Maintenance & Reliability Professional (CMRP)
The CMRP certification serves as a benchmark for maintenance and reliability professionals. It focuses on ensuring knowledge in reliability, maintenance management, and asset management. Professionals with CMRP certification benefit from enhanced credibility, career advancement opportunities, and alignment with industry best practices. This certification equips individuals to implement maintenance strategies that reduce costs and increase equipment uptime, ultimately contributing to organizational success.
Certified Maintenance & Reliability Technician (CMRT)
The CMRT certification is designed for technicians demonstrating expertise in the maintenance and reliability field. It validates skills necessary for daily maintenance tasks and reliability improvements. Obtaining CMRT certification leads to better job performance, recognition, and the practical application of maintenance knowledge to enhance equipment efficiency and reliability.
Association of Equipment Management Professionals (AEMP)
AEMP offers certifications such as Equipment Management Specialist (EMS), Certified Equipment Manager (CEM), and Certified Equipment Support Professional (CESP), focusing on equipment maintenance and reliability management. These certifications ensure professionals are adept at managing fleets, implementing effective maintenance strategies, and optimizing equipment lifecycle, thereby enhancing operational efficiency and cost-effectiveness.
Equipment Management Specialist (EMS)
EMS certification specializes in equipment management, emphasizing strategic asset management and maintenance planning. It prepares individuals to make data-driven decisions regarding equipment maintenance, leading to improved asset management and operational efficiency.
Certified Equipment Manager (CEM)
CEM certification recognizes professionals who excel in managing heavy equipment fleets and maintenance operations. CEM-certified managers contribute to reducing operational costs, improving equipment utilization, and ensuring compliance with safety and environmental regulations.
Certified Equipment Support Professional (CESP)
CESP certification targets individuals supporting the equipment management process, including parts and service managers. CESP certification enhances one’s ability to support maintenance strategies, improve customer service, and ensure the effectiveness of maintenance operations.
Examples of Equipment Maintenance
We have explored various industries and have found significant examples where effective equipment maintenance has not only prevented equipment failures but also led to substantial financial savings:
Digital Work Management in the Chemicals Industry
A global chemicals company integrated a Digital Work Management (DWM) system with its existing ERP platform, significantly transforming its maintenance planning, scheduling, and work execution. This change resulted in a 30% increase in productivity within the maintenance planning and scheduling department and a doubling of maintenance tasks completed on schedule. The implementation of DWM technology, by optimizing job planning and execution, led to cost reductions of 15 to 30 percent through increased efficiency of maintenance labor and reduced planned downtime.
Predictive Maintenance in the Oil and Gas Industry
An offshore oil and gas operator introduced a sophisticated Predictive Maintenance (PdM) system across its platforms, using data from 30 years of operations. This approach resulted in a 20 percent reduction in downtime and production increases equivalent to more than 500,000 barrels of oil annually. The implementation involved developing over 500 advanced analytics models to identify and prevent failures, highlighting the effectiveness of high-maturity PdM approaches.
Predictive Maintenance at Duke Energy Renewables
Duke Energy Renewables applied advanced analytics and machine learning to automate the detection of failing contactors on wind turbines. This trial not only reduced maintenance costs and improved uptime but also allowed better management of spare parts inventory. By automating the prediction of impending failure, the company could proactively maintain turbines, with the potential financial savings amounting to hundreds of thousands of dollars per event.
Global Mining Company’s Use of Predictive Maintenance
A leading global mining company utilized AI software to predict and prevent failures in its material transport operations. By analyzing telematics data, the company gained advanced notice of issues, allowing for proactive maintenance. This strategy led to a reduction in single-car unscheduled maintenance events by an estimated 50 percent, translating into approximately $34 million in savings over five years.