What is Predictive Maintenance? Everything You Need to Know
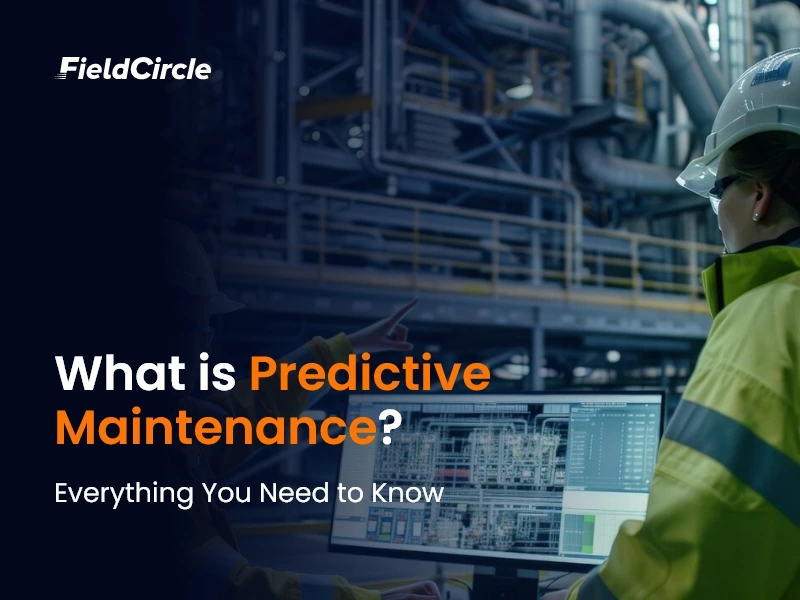
Predictive maintenance (PdM) is a condition-based monitoring approach that uses real-time data to assess equipment health and determine the optimal time for maintenance.
This strategy leverages IoT sensors, advanced analytics, and machine learning to analyze real-time data stored in centralized systems. By generating predictive alerts, PdM helps maintenance teams schedule proactive repairs, reducing downtime and extending asset lifespans. Tools like Computerized Maintenance Management Systems (CMMS) assist in this process through various ways.
Specific methods in PdM include vibration analysis, oil condition monitoring, ultrasonic testing, and current and power monitoring.
While PdM requires investments in sensors, software, and team training, its benefits are substantial. It has become a vital maintenance strategy in most industries including manufacturing, energy, and transportation.
PdM is a vast area and each dimension of it needs careful exploration which we achieve via this informative blog. Read it and understand how PdM is a highly effective maintenance strategy to take your maintenance function to the next level.
How Does Predictive Maintenance Work?
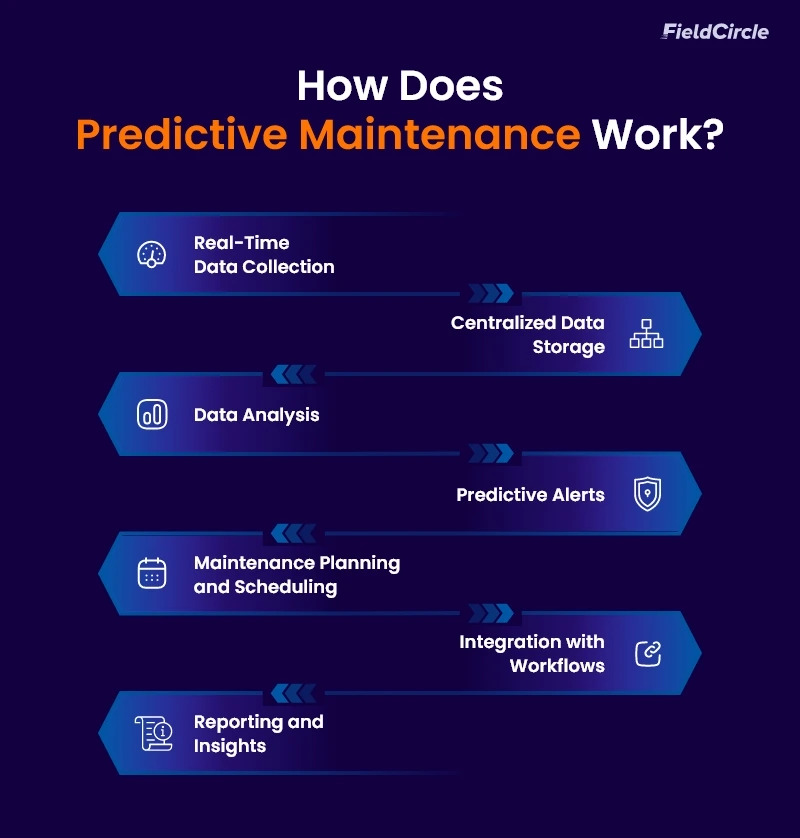
Predictive maintenance works by collecting real-time data through sensors in a centralized storage system to analyze and predict potential failures for proactive intervention. The step-by-step working process of predictive maintenance is given below:
- Real-Time Data Collection:
- Centralized Data Storage:
- Data Analysis:
- Predictive Alerts:
- Maintenance Planning and Scheduling:
- Integration with Workflows:
- Reporting and Insights:
PdM embeds sensors in equipment like IoT devices to collect critical and accurate real-time data, such as temperature, vibration, pressure, and operating speed. This provides the foundation for accurate prediction.
The data collected from IoT sensors and devices is transmitted to a centralized data storage or cloud storage system. This provides an organized single-source platform for data analysis, enabling seamless integration with analysis tools and predictive models.
PdM analyzes collected data using predictive analytics and machine learning algorithms to detect trends, patterns, and anomalies. It uses advanced models to compare real-time and historical data to identify early signs of wear or failure.
After detecting a risk, the maintenance system alerts the maintenance teams about the required intervention. Maintenance software, such as a Computerized maintenance management system (CMMS), sends alerts via dashboards, email, or mobile app notifications.
PdM analyzes real-time data about equipment health to predict failure timelines using AI tools, CMMS or ERP integration and schedule maintenance tasks. Planned interventions optimize resources, increase uptime, and enhance cost efficiency.
Predictive maintenance integrates with workflows using computerized maintenance management software (CMMS) and ERP systems to streamline operations. It includes automating and scheduling task assignments, inventory management, and updating maintenance logs.
PdM summarizes asset performance, equipment health, maintenance trends, and failure predictions into detailed reports. These reports provide actionable insights for decision-making, and help identify recurring issues.
What Are the Types of Predictive Maintenance?
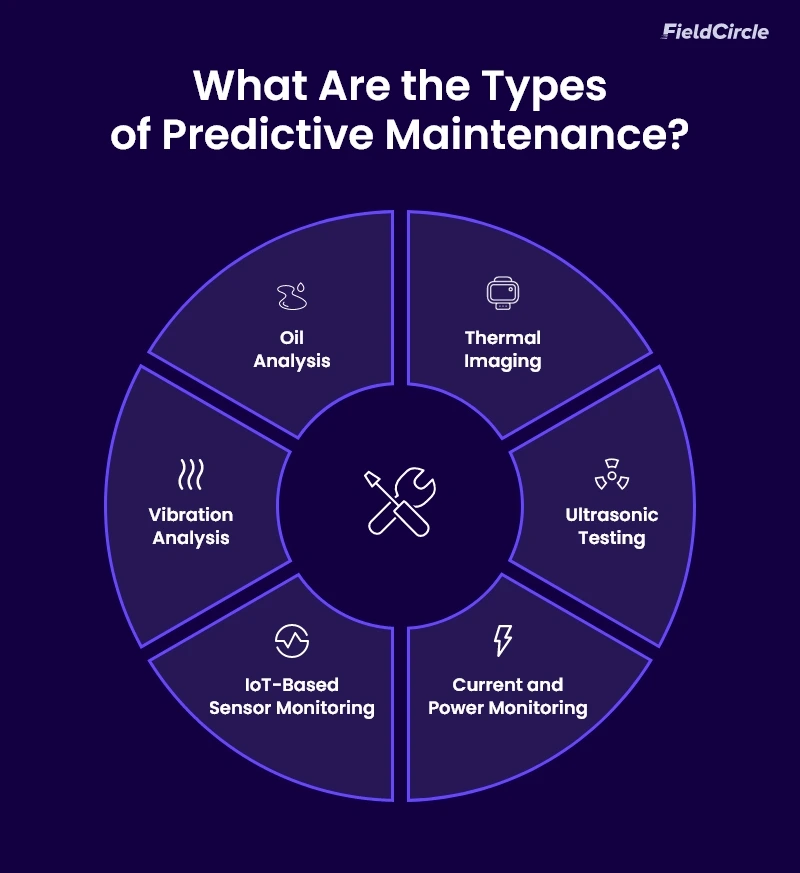
Types of predictive maintenance range from IoT-based sensor monitoring to thermal analysis and current and power monitoring. PdM implements advanced methods and technologies to monitor equipment health and predict potential failures.
6 main types of predictive maintenance are
- IoT-Based Sensor Monitoring
- Vibration Analysis
- Oil Analysis
- Thermal Imaging
- Ultrasonic Testing
- Current and Power Monitoring
- IoT-Based Sensor Monitoring:
- Vibration Analysis:
- Oil Analysis:
- Thermal Imaging:
- Ultrasonic Testing:
- Current and Power Monitoring:
Parameters such as temperature, vibration, humidity, and pressure are monitored using IoT devices that collect real-time data and transmit it to central storage through an IoT network. These sensors help detect anomalies and predict failures, making them suitable for manufacturing plants, power grids, and HVAC systems. This predictive maintenance type enables real-time monitoring, reduces manual inspections, minimizes downtime, and increases the accuracy of maintenance predictions.
Machinery vibration patterns are monitored and analyzed to detect imbalances, misalignments or bearing issues. Vibration sensors measure vibration frequency and amplitude, which are analyzed to detect potential failures early and reduce unplanned downtime. Commonly used in rotating equipment such as motors, turbines, pumps and compressors, vibration analysis ensures smooth operations, extends equipment life, increases safety and improves maintenance efficiency.
Lubricant quality and composition are evaluated using oil analysis to detect contamination, wear particles or chemical degradation. It is mainly used in automotive, manufacturing and energy industries to monitor engines, gearboxes, turbines and hydraulic systems. It uses advanced tools and sensors to analyze oil’s chemical and physical properties for contaminants, viscosity, oxidation and metal particles. This optimizes oil change intervals, detects early signs of equipment wear, extends asset life, reduces maintenance cost, and minimizes production halt.
Using infrared cameras, thermal imaging detects heat patterns and temperature variations in equipment. It shows heat signatures and hotspots that indicate overheating, friction, electrical failure, or potential failure points. Common in electrical panels, motors, power transformers, and HVAC systems, thermal imaging prevents equipment failure by spotting early signs of wear and tear, enhances safety and system reliability, and minimizes downtime and maintenance costs.
High-frequency sound waves are transmitted into materials, and reflections are analyzed to detect structural abnormalities and inconsistencies. Ultrasonic testing is used in pipelines, pressure vessels, and structural components across industries such as oil and gas, aerospace, and construction. It detects cracks, corrosion, or thinning in pipes, tanks, and machinery, as well as leaks in compressed air, gas, or steam systems. It also prevents catastrophic failures and ensures workplace safety.
Real-time electrical parameters like voltage, current, and power factor are measured and analyzed to detect overloads, inefficiencies, and impending electrical failures. This type of predictive maintenance is applied to motors, pumps, compressors, generators, lighting, and other electrical systems. It prevents unexpected shutdowns, reduces energy consumption, improves power quality, optimizes power capacity, enhances operational efficiency, and reduces operational costs.
When Should Predictive Maintenance Be Used?
Predictive maintenance should be used for rotating machinery, pumps, valves, electrical equipment, HVAC systems, and other suitable assets that can provide measurable performance data. It is an effective maintenance management strategy suitable for expensive assets that significantly impact operations and are costly to replace.
Suitable Assets for PdM
- Rotating Machinery: Motors, turbines, compressors, and fans.
- Pumps and Valves: Fluid-handling systems prone to wear.
- Electrical Equipment: Transformers, circuit breakers, and generators.
- HVAC Systems: Heating, ventilation, and cooling units.
- Production Lines: Conveyor belts, robotic arms, and assembly machines.
- Vehicles and Fleet Equipment: Trucks, forklifts, and transport machinery.
- Heavy Machinery: Excavators, cranes, and mining equipment.
- Utility Systems: Boilers, chillers, and power distribution networks.
Unsuitable Assets for PdM
- Low-Cost Equipment: Inexpensive and easily replaceable assets.
- Non-Critical Assets: Systems whose failure does not impact overall operations significantly.
- Unpredictable Failures: Equipment that fails without warning or measurable wear indicators.
- Short Lifespan Assets: Disposable items or components designed for short-term use.
- Limited Data Capability: Machines without sensors or the ability to provide measurable performance data.
- Highly Manual Equipment: Tools or assets with minimal moving parts and wear.
Who Utilizes Predictive Maintenance?
Industries like manufacturing, energy, transportation, oil and gas, facilities management, healthcare, agriculture, automotive, and construction utilize predictive maintenance. PdM is a versatile solution to improve operational efficiency, prevent unplanned breakdowns, and reduce maintenance costs.
- Manufacturing:
- Energy and Utilities:
- Transportation and Logistics:
- Oil and Gas:
- Facilities Management:
- Healthcare:
- Agriculture:
- Automotive:
- Mining and Construction:
Being proactive in maintenance is key to service efficiency in manufacturing. Predictive maintenance is a key part of that strategy as its adoption can aid in seamless operation of critical machinery, such as conveyors, presses, and CNC machines, by continuously monitoring their condition. It detects wear and tear in motors, bearings, and pumps using vibration analysis and real-time tracking, allowing for early intervention. It also optimizes energy efficiency in large-scale production lines, reducing operational costs.
Predictive maintenance in energy and utilities monitors turbines, generators, circuit breakers, and transformers using thermal imaging and current analysis to detect early faults. It also predicts maintenance for grid infrastructure, helping to prevent outages and ensure a steady power supply. By optimizing energy efficiency and resource utilization, PdM minimizes costly system failures and supports uninterrupted power generation and distribution.
In the transportation and logistics sector, predictive maintenance enhances the reliability of fleet vehicles, including trucks, trains, ships, and aircraft, by monitoring engine health, tire pressure, and fuel efficiency. It predicts wear on critical components such as brakes, bearings, and suspension systems, preventing mechanical failures. Additionally, it ensures the smooth operation of warehouse equipment like conveyors and forklifts, reducing operational disruptions.
The oil and gas industry uses predictive maintenance to monitor pumps, pipelines, and drilling equipment and vibration analysis for compressors to identify wear and tear. Using ultrasonic testing, it detects leaks, corrosion, and pressure anomalies in real-time. By optimizing maintenance schedules and improving compliance with industry regulations, PdM reduces costly unplanned downtime, minimizes environmental hazards, and enhances overall operational reliability.
Predictive maintenance ensures uninterrupted operation of critical building systems, including HVAC, lighting, and elevators, for tenant satisfaction and safety. It uses IoT-based monitoring to oversee HVAC systems for efficiency and wear, predict failures in electrical and lighting systems, and maintain plumbing, fire suppression systems, and elevators to prevent costly breakdowns.
In the healthcare sector, predictive maintenance monitors diagnostic and critical medical equipment (MRI machines, ventilators) for wear and performance issues. It helps maintain HVAC systems in hospitals to ensure optimal air quality and infection control for seamless operations. PdM also manages backup power systems to guarantee uninterrupted operations during outages and avoid disruptions in patient care.
Predictive maintenance monitors tractors, irrigation systems, and storage facilities to predict machinery wear and tear and schedule timely repairs. It also optimizes resources, including fuel, water, and fertilizers, to improve efficiency and reduce maintenance costs. PdM ensures the optimal performance of automated systems like drones and smart irrigation setups to enhance yield quality.
The automotive industry relies on predictive maintenance to enhance vehicle reliability and safety by proactively scheduling fleet servicing. Telematics and IoT sensors monitor the condition of critical components, such as brakes and suspension, to predict potential failures. PdM supports manufacturing operations by monitoring assembly lines, robotic welders, and painting booths, ensuring high production quality and minimal downtime.
For the mining and construction industry, predictive maintenance monitors excavators, cranes, and drilling equipment for wear and tear using vibration analysis and ultrasonic testing. It tracks conveyor belts, crushers, and other key equipment for potential failures and ensures optimal performance of power systems and hydraulic components.
What Are the Benefits of Predictive Maintenance?
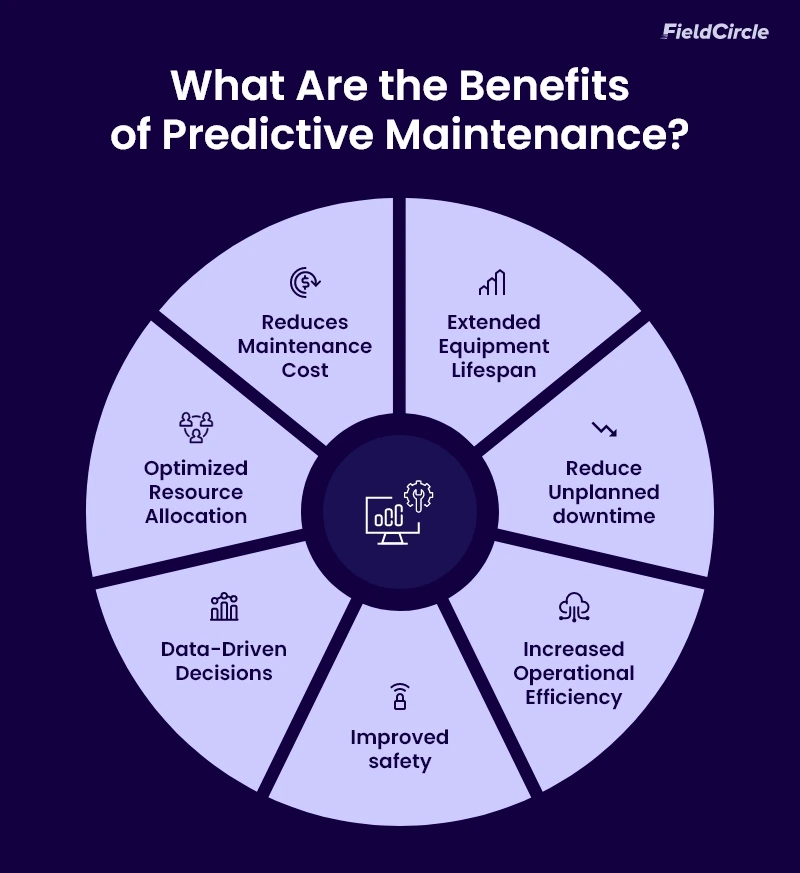
The benefits of predictive maintenance range from reducing repair and replacement costs to minimizing unplanned breakdowns, improving workplace safety, and maximizing resource utilization. PdM offers a transformative approach to equipment management that provides proactive and data-driven solutions.
Top 7 benefits of predictive maintenance are
- Reduces Maintenance Cost
- Extended Equipment Lifespan
- Reduce Unplanned downtime
- Increased Operational Efficiency
- Improved safety
- Data-Driven Decisions
- Optimized Resource Allocation
1. Reduces Maintenance Cost
Preventive maintenance reduces maintenance costs by using real-time monitoring to identify issues early and minimize downtime and the need for expensive emergency repairs. For example, a major processed food manufacturer implemented AI-based predictive maintenance to monitor key equipment performance and experienced a >30% reduction in maintenance costs.
This is how predictive maintenance enables condition-based maintenance to avoid unnecessary routine checks. Optimizing resource allocation of labor and spare parts and extending equipment lifespan lowers operational and replacement costs.
2. Extended Equipment Lifespan
Preventive maintenance reduces equipment wear and tear and extends its lifespan by continuously monitoring assets and ensuring they operate optimally. It also prevents severe damage and minimizes overloading and inefficiencies. By maximizing equipment life, preventive maintenance delays the need for costly replacements, maintains consistent performance, and increases ROI up to >10 times.
3. Reduce Unplanned Downtime
PdM reduces unplanned downtime by addressing issues before they escalate and significantly impact operations, preventing unexpected failures. It enables proactive repairs and maintenance scheduling to minimize unexpected equipment breakdowns and ensure continuous operations, improving productivity and reliability.
For example, Baxter implemented predictive maintenance using Amazon Monitron, which helped them avoid 500 hours of unplanned downtime. By reducing unplanned downtime, preventive maintenance saves repairs related to emergency repairs and operational delays.
4. Increased Operational Efficiency
Preventive maintenance increases operational efficiency by minimizing unplanned downtime, optimizing maintenance schedules, and enhancing equipment performance. For instance, a chemical producer deployed predictive diagnostics and decreased the troubleshooting times by nearly >50%.
This way, predictive maintenance streamlines operations with fewer disruptions, reduces operational costs through better resource utilization, and improves productivity and overall system reliability by reducing unnecessary interventions and identifying inefficiencies.
5. Improved Safety
PdM improves safety by identifying and addressing potential equipment failures before they occur, reducing the risk of accidents and workplace hazards. For instance, a railway network with excessive wear on rails and tracks used an onboard monitoring system to measure track vibration and deformation to reduce derailment incidents by >60%.
It ensures that machinery operates with safe parameters by monitoring critical metrics like temperature and vibration. Preventive maintenance protects works by preventing hazardous conditions, promotes compliance with safety regulations and standards, and minimizes risks in high-stakes environments.
6. Data-Driven Decisions
Preventive maintenance uses real-time and historical data via advanced analytics to make informed decisions about maintenance strategies and investments. By continuously monitoring key maintenance metrics, you can identify patterns and trends to predict equipment failures, optimize maintenance schedules, reduce unnecessary repairs, improve resource allocation, and support long-term planning by providing actionable insights.
For example, General Electric implemented predictive maintenance solutions to analyze sensor data from industrial equipment. This helped them reduce unscheduled maintenance by >30% and increase operational efficiency by 15%.
7. Optimized Resource Allocation
PdM optimizes resource allocation by efficiently organizing and distributing manpower, tools, and spare parts and proactively addressing maintenance needs. It also aligns resources with requirements to reduce unnecessary maintenance tasks and overstocking of spare parts. A McKinsey study showed that utilizing AI-driven maintenance improves parts availability by >20-30% and reduces inventory holding costs by 5-20%. It minimizes costs by targeting resources only when needed and improves overall resource utilization for productivity and operational efficiency.
What Challenges Are Associated with Predictive Maintenance?
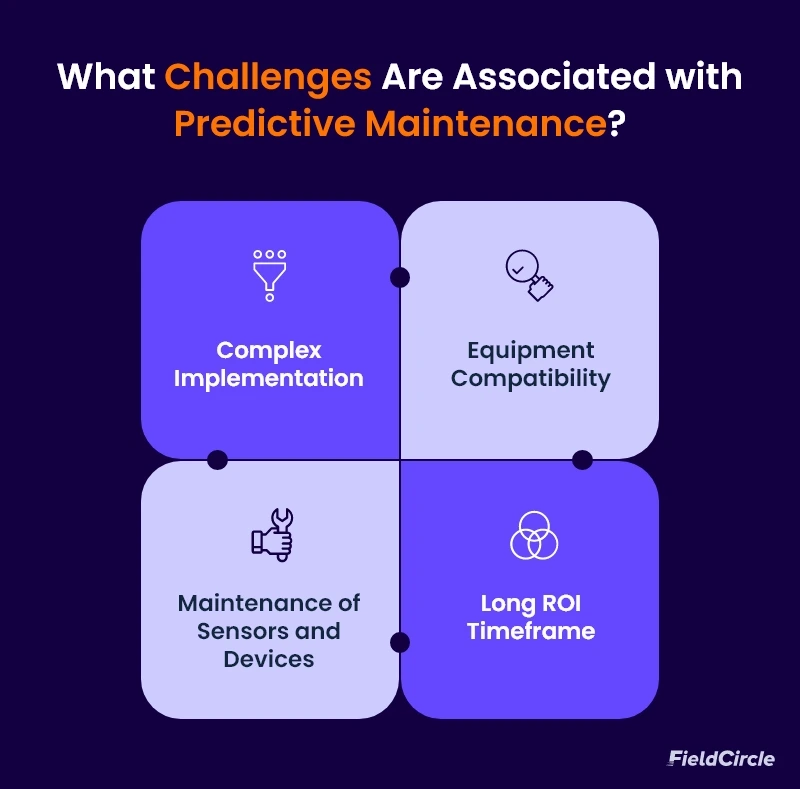
The challenges associated with predictive maintenance include complex implementation, equipment compatibility, sensor and device maintenance, and a long ROI timeframe. Tackling these challenges requires careful planning and resource allocation.
Complex Implementation
Implementing predictive maintenance requires integrating sensors, IoT devices, machine learning models, and analytics tools into existing systems. It also requires experts in hardware, software, and network integration. If the implementation process is misaligned or poorly set up, it reduces the accuracy and reliability of maintenance predictions. A phased rollout plan, collaboration with experienced vendors or consultants, and team training for long-term maintenance are necessary to mitigate this.
Equipment Compatibility
Many legacy systems or non-IoT-enabled equipment lack the necessary sensors or connectivity for PdM. This incompatibility between systems or software hinders data integration, creating data gaps that limit the effectiveness of predictive maintenance. It also increases costs and delays, leaving critical assets unmonitored. Device compatibility can be achieved by investing in newer, PdM-compatible equipment where economically feasible. Organizations must gradually upgrade equipment to ensure seamless compatibility across assets.
Maintenance of Sensors and Devices
Sensors and IoT devices can fail, degrade, or lose calibration over time. Environmental factors like dust, heat, and vibration impact their performance, leading to inaccurate data collection, faulty analysis, false alerts, or missed predictions. Delays in identifying potential failures also increase the risks of reduced uptime. Proper maintenance requires regular inspection and calibration schedules for all devices. Using robust and high-quality sensors helps minimize the risk of failure.
Long ROI Timeframe
PdM implementation requires a significant initial investment in sensors, software, and training, where ROI may take years to materialize. This slows down the adoption of PdM and results in investor reluctance. Organizations should start with scalable pilot projects to demonstrate their value as a countermeasure. They make phased investments to manage costs and focus on high-impact equipment to accelerate ROI.
How Does Predictive Maintenance Compare to Preventive Maintenance?
Predictive maintenance is condition-based and uses real-time data, IoT sensors, and advanced analytics to predict potential failures before they happen so you can intervene, whereas preventive maintenance is time-based and schedules regular inspections and repairs at set intervals regardless of the asset’s condition.
Predictive maintenance is more dynamic and cost-effective, as it optimizes maintenance based on actual equipment performance, extends asset life, and reduces unplanned downtime. Preventive maintenance is simpler to implement and works for assets with predictable wear and tear, but it is less efficient because it doesn’t account for real-time conditions. Organizations choose predictive maintenance for critical systems where downtime poses the most significant risk, while preventive maintenance is typically used for simpler or less critical equipment.
Why Is Predictive Maintenance Important for Asset Lifespan?
Predictive maintenance is vital for asset lifespan because it prevents equipment wear and tear, optimizes usage, minimizes severe failures, reduces unnecessary maintenance, and enhances operating conditions. It deploys data-driven strategies to maximize performance and minimize long-term costs.
- Prevents Excessive Wear and Tear:
- Optimizes Usage:
- Minimizes Severe Failures:
- Reduces Unnecessary Maintenance:
- Improves Lubrication and Calibration:
- Enhances Operating Conditions:
- Supports Data-Driven Decision-Making:
- Increases Reliability:
- Encourages Sustainable Practices:
- Protects Investment:
Regular monitoring relieves stress on components by identifying and addressing the issues early. This proactive approach extends the life of the equipment by preventing progressive damage.
Predictive maintenance keeps the equipment running at its best by avoiding overloading, which causes wear and tear, and underutilization, which causes degradation. Balanced use means assets perform consistently over time.
Minor issues like vibrations or temperature fluctuations are caught early so they don’t escalate into big problems. This reduces the risk of major failures that could permanently damage the asset.
Predictive maintenance eliminates unnecessary maintenance by fixing maintenance based on real-time data. This avoids over-maintenance, preserves the asset, and reduces the costs of excessive interventions.
Oil changes, recalibrations, and other adjustments are made as needed rather than on a schedule. This results in optimal performance, less friction, and no wear on moving parts.
Predictive maintenance identifies unfavorable conditions affecting performance, such as heat, moisture, or vibration. By mitigating these conditions, organizations create a stable and favorable operating environment for their assets.
Asset performance insights enable organizations to make informed maintenance planning and operational strategy decisions. Long-term maintenance schedules can be refined to match the asset’s actual needs.
Continuous monitoring and timely maintenance intervention ensure equipment runs for life. This reduces failures and builds confidence in asset performance.
Predictive maintenance reduces the need for frequent replacements by extending asset life. This reduces resource consumption and supports green and sustainable operations.
Predictive maintenance gives a strong ROI by maximizing the productive life of high-value assets. Businesses must allocate resources better to reduce replacement and repair costs.
Build a Predictive Maintenance Strategy with FieldCircle
With its extensive list of features, FieldCircle’s predictive maintenance software is an effective tool for building predictive maintenance. Combining IoT sensors, real-time monitoring, and predictive analytics, it leverages multiple capabilities to raise the standard of your maintenance operations.
Additionally, the application’s ability to integrate seamlessly with other enterprise systems makes it a versatile solution. The centralized nature combined with state-of-the-art predictive analytics makes our tool the best companion for building a full-spectrum predictive maintenance program.