Most Common Preventive Maintenance Examples Across Major Industries
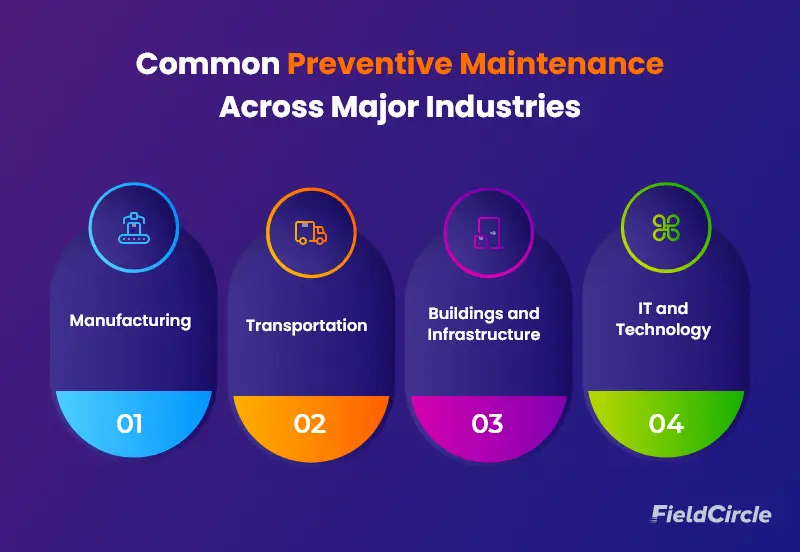
Preventive maintenance is a proactive maintenance strategy approach where maintenance actions are performed in time before equipment has shown any sign of malfunctioning. From downtime curtailment, reliable and continuous operations to extended asset life, the innumerable benefits of preventive maintenance have prompted industries across the board to divert their focus from reactive maintenance to building a long-term preventive maintenance (PM) program.
As a result, preventive maintenance has become a key lever for many industries which are actively using it to keep the value chain intact and achieve operational excellence. In the ensuing discussion, we cast light on the following industries:
- Manufacturing
- Transportation
- Buildings and Infrastructure
- IT and Technology
To go into the practicalities, we discuss specific examples of preventive maintenance (PM) across these industries which explain how the PM program is executed.
What are the well-known Examples of Preventive Maintenance?
Following are the examples that explain how preventive maintenance is performed across industries. During the process, the maintenance team adheres to maintenance schedule, follows requisite checklists and compliances to carry it successfully as we see.
Manufacturing
From assembly lines to packaging systems, preventive maintenance in manufacturing is important for minimizing disruptions. We discuss how preventive maintenance is applied across different systems.
- Conveyor Belts
- CNC Machines
- Hydraulic Systems
- Electrical Systems
These examples of preventive maintenance (PM) in manufacturing explain how the PM program makes machinery operate at peak performance. A manufacturing maintenance software aids in this process:
- Conveyor Belts
Conveyor belts are the backbone of material logistics operations in manufacturing, as they carry out a seamless movement of raw materials and finished products across different stages of production. For instance, in steel manufacturing, conveyor belts transport heavy raw materials such as iron ore and coal to blast furnaces, while in cement manufacturing, they handle abrasive substances like limestone and clinker. Their efficiency directly impacts production timelines and overall operational costs. Regular manufacturing maintenance is essential to ensure these systems remain reliable. Time-based maintenance is a type of preventive maintenance that is important in this case. The maintenance team performs following actions to keep conveyor belts in optimal condition:
- Remove debris and dust from the belt surface.
- Perform cleaning using specialized systems like rotary brushes or high-pressure air.
- Apply non-abrasive cleaning agents to avoid chemical damage.
- Lubricate bearings, rollers, and other moving components.
- Inspect belt splices for wear and damage.
- Adjust belt tracking alignment using laser-guided tools.
- Check and replace clogged filters in the system.
- Examine pulleys and rollers for signs of wear.
- Verify and maintain proper belt tension.
- Inspect the tracking system for misalignments.
- Monitor and replace worn-out or damaged belts.
- Tighten loose fasteners and connections.
- CNC Machines
Controlled by pre-programmed software, CNC machines are used to shape materials such as metal, plastic, and wood into intricate components. However, their precision can be compromised if they are not maintained. Preventive maintenance for CNC machines focuses on both mechanical and software components to keep them running smoothly. The process includes the following activities:
- Remove chips and debris from machine enclosures to prevent interference with moving parts.
- Inspect tools for microscopic cracks or wear using a specialized piece of equipment like microscope.
- Check coolant levels, replacing contaminated fluids and filters as needed.
- Test axis alignment and backlash using dial indicators or laser alignment systems to ensure precise movements.
- Inspect electrical connections and repair them – if out of order – to mitigate risks of power inconsistencies.
- Update firmware and calibrate control systems to maintain optimal performance.
- Test emergency stop systems regularly for operator safety.
- Hydraulic Systems
These systems are integral to various industrial operations, where they provide the power needed for heavy lifting and precise movements. The complexity and sensitivity of hydraulic systems make preventive maintenance essential to avoid unexpected failures that could disrupt production and incur substantial repair costs. In preventive maintenance for hydraulic systems the maintenance staff members:
- Perform fluid analysis using particle counters and sampling kits to detect contaminants such as water, air, or metallic particles.
- Conduct pressure testing of hoses to identify leaks or weaknesses, replacing damaged hoses promptly.
- Examine seals and O-rings for signs of degradation caused by thermal stress or fluid incompatibility.
- Clean reservoirs to eliminate sediment buildup and replace breather filters to block airborne contaminants.
- Inspect heat exchangers to ensure efficient heat dissipation and prevent overheating.
- Electrical Systems
It is impossible to imagine operations without electrical systems being in order. They power machines and equipment across various processes in manufacturing and maintain the operational continuity. Regular preventive maintenance ensures uninterrupted operations and also extends the lifespan of the equipment. Maintenance tasks include the following:
- Use thermal imaging cameras to detect hotspots from loose connections or overloaded circuits.
- Test circuit breakers with secondary injection test sets to confirm their tripping functionality.
- Clean electrical panels using non-conductive cleaning agents to minimize the risk of short circuits.
- Verify the reliability of protective relays through regular testing.
- Inspect cables for insulation damage and replace worn-out sections to maintain system integrity.
Transportation
Following are the three different types of transportation mediums – which are important in the transportation industry for both passenger and commercial transportation.
- Vehicles
- Trains
- Aircraft
Let’s see how preventive maintenance of these various transportation mediums is performed to maintain continuity in the logistics sector.
- Vehicles
The movement of goods and people across vast distances cannot take place if the fleet is not maintained. The performance, safety, and efficiency of vehicles are directly tied to how well they are maintained. Preventive maintenance for vehicles involves a structured approach to minimize unplanned downtime, improve fuel efficiency, and enhance overall reliability. Following are the maintenance works which ensure that vehicles remain roadworthy.
- Conduct oil changes based on mileage or engine hour metrics, using viscosity analyzers to assess oil condition.
- Inspect and replace engine air filters to prevent contaminants from affecting fuel efficiency.
- Check brake systems for wear by measuring rotor thickness and assessing pad material integrity.
- Perform tire inspections, including tread depth measurements with tread wear indicators and wheel alignment checks using computerized systems.
- Extend fluid checks to transmission, differential, and power steering systems, replacing fluids as per manufacturer guidelines.
- Test battery voltage and load capacity with battery analyzers to prevent power failures.
- Inspect belts and hoses in the engine bay for cracks or leaks, and replace them proactively to avoid breakdowns.
- Aircraft
Aircraft maintenance is governed by stringent regulations to ensure passenger safety and operational efficiency. These machines operate under extreme conditions, which makes preventive maintenance essential to keep compliant with aviation standards. In the preventive maintenance process, the aircraft maintenance team members:
- Use borescopes to inspect airframes for internal structural issues like corrosion or cracks.
- Perform boroscopic inspections of engines to examine turbine blades and combustion chambers for wear or damage.
- Lubricate moving parts, such as landing gear joints, with aviation-grade lubricants designed for extreme conditions.
- Replace worn components, such as seals and gaskets, using certified parts approved by regulatory authorities.
- Test flight control systems, including flaps and ailerons, to ensure proper movement and response.
- Inspect avionics systems, applying software updates to mitigate vulnerabilities and improve performance.
- Trains
Addressing both mechanical and electrical systems is necessary to prevent service disruptions and prolong the lifespan of critical components in trains. Preventative maintenance tasks for trains focus on maintaining safety, efficiency, and reliability and include the following activities where the maintenance function:
- Inspects wheelsets using ultrasonic testing to detect internal flaws that could lead to cracks.
- Grinds wheels regularly to prevent flat spots and maintain a smooth rolling surface.
- Performs track inspections with track geometry cars equipped with lasers and sensors to identify irregularities.
- Replaces worn brake pads and inspect pneumatic brake lines for potential leaks.
- Tests electrical systems like traction motors for insulation resistance to ensure reliability under load conditions.
Buildings and Infrastructure
In buildings and infrastructure, preventive maintenance is performed to maintain the functionality of the following equipment to ensure the safety and comfort of occupants.
- HVAC Systems
- Plumbing Systems
- Electrical Systems
- Elevators and Escalators
The following examples explain how by regularly servicing key systems, building owners keep expensive repairs at bay, minimize disruptions, and also adhere to safety regulations.
- HVAC Systems
The indoor comfort and energy efficiency in buildings is maintained through heating, ventilation, and air conditioning (HVAC) systems. These systems regulate temperature, airflow, and humidity, making them indispensable for residential, commercial, and industrial spaces. Maintenance activities focus on keeping components clean, aligned, and responsive to control commands through:
- Replacing filters to prevent blockages that could restrict airflow and strain motors.
- Cleaning coils with coil cleaning solutions to sustain efficient heat exchange.
- Inspecting belts and motors for wear using belt tension meters and vibration analysis tools.
- Calibrating control systems to maintain accurate temperature and humidity levels, testing sensors for responsiveness.
- Checking drain lines for clogs to prevent water damage and inhibit mold growth.
- Plumbing Systems
Plumbing systems are responsible for water distribution and waste management in buildings. They require regular maintenance to ensure smooth operation and avoid disruptions caused by leaks, clogs, or structural issues. These systems are kept in shape through preventive maintenance program performed through the following actions:
- Use acoustic sensors to detect hidden leaks in pipes.
- Conduct drain inspections with cameras to identify obstructions or structural damage.
- Test valve operation to confirm proper flow control, replacing aging valves with high-performance models.
- Inspect seals and gaskets for wear or hardening due to temperature variations or chemical exposure.
- Electrical Systems
Like manufacturing, even buildings are dependent on electrical systems as they transmit power for operating various equipment used for functioning of the facility operations and devices used by occupants. Preventive maintenance minimizes risks such as equipment failure, overheating, or electrical shocks while extending the lifespan of electrical. The maintenance team conducts following actions to keep electrical systems smoothly functioning:
- Perform load testing of backup generators to guarantee reliable performance during outages.
- Clean and lubricate switchgear to maintain smooth operation and prevent overheating.
- Test cables with insulation resistance meters to identify potential faults.
- Inspect surge protection devices, replacing them if they fail to provide adequate protection against voltage spikes.
- Verify grounding systems to ensure safety and reduce the risk of electrical shocks.
- Elevators and Escalators
In multi-storey structures, where people need to move across the building, the seamless functioning of elevators and escalator systems makes the whole difference. In the preventive maintenance of these building equipment, the maintenance team addresses issues mechanical and electrical components by
- Lubricating moving parts, such as bearings and gears, to minimize wear and noise.
- Testing safety devices, including overspeed governors and emergency brakes, using specialized equipment.
- Inspecting control panels to confirm proper functioning of electrical components.
- Adjusting leveling systems to ensure elevator floors align accurately with building levels.
- Implementing corrective maintenance for checking and correcting step alignment and chain tension in escalators to maintain smooth operation.
IT and Technology
Preventive maintenance in IT covers both: hardware upkeep to software updates. Specifically these components are:
- Servers
- Network Equipment
- Desktop Computers
Maintenance of these equipment is important to minimize system outages, safeguard against cyber threats, and prolong the longevity of technological infrastructure, as discussed below.
- Servers
The disruption of servers can lead to significant financial and reputational damage for a business. In preventive maintenance for servers, the IT teams carry out hardware, software, and security updates by:
- Applying firmware and software updates to address vulnerabilities and improve system performance.
- Testing power supply units and monitoring fan speeds to prevent equipment failure due to overheating.
- Conducting automated data backups to protect critical information and maintain business continuity.
- Checking disk arrays for RAID (Redundant Array of Independent Disks) integrity and replacing failing drives to sustain redundancy.
- Applying security patches to defend against emerging cyber threats and minimize risks.
- Network Equipment
Network equipment, such as routers, switches, and modems, enables seamless data transmission and communication. Preventive maintenance tasks focus on optimizing configurations, maintaining hardware components, minimizing latency and reducing the likelihood of connection failures as highlighted through the following activities:
- Update firmware to address bugs and add new features that enhance functionality.
- Create configuration backups to preserve system settings and enable quick recovery in case of issues.
- Use usage-based maintenance through performance monitoring tools to analyze bandwidth usage and identify potential bottlenecks.
- Clean optical ports and replace damaged cables to maintain high-quality connections.
- Test power supplies for routers and switches, scheduling replacements to prevent unexpected failures.
- Desktop Computers
From managing data to running resource-intensive software, desktop computers provide the processing power and reliability essential for business operations. They support a wide range of activities, including communication, collaboration, data analysis, and customer service, and are integral to both productivity and decision-making. The preventive maintenance program focuses on monitoring the health of desktop computers and maintain their longevity where the IT personnel:
- Perform regular disk cleanup to remove temporary files and improve storage efficiency.
- Conduct antivirus scans to detect and remove malicious software, protecting system integrity.
- Inspect internal components, such as RAM and processors, for overheating using thermal imaging tools.
- Remove dust from internal components using compressed air to enhance cooling and prevent hardware degradation.
- Test peripheral devices like keyboards and mice for functionality and update outdated drivers to maintain compatibility.
It’s Time you build a Preventive Maintenance program with a CMMS
Crafting a preventive maintenance strategy with a computerized maintenance management system (CMMS) software shifts maintenance operations from being reactive to truly proactive – a positive step towards predictive maintenance. Instead of responding to breakdowns, you create a methodical structure to implement your maintenance program.
Start by identifying all critical assets and mapping out their maintenance needs. Using FieldCircle CMMS can be a great step here. It will help establish workflows, set priorities, and create a practical preventive maintenance plan that aligns with operational demands. Use it to streamline inventory management and sustain the levels of spares so that there are no disruptions to maintenance operations.
Over time, the analytics offered by our preventive maintenance software helps uncover patterns, and allow your team to adjust its approach and tackle inefficiencies. This way you will streamline routine maintenance and improve the maintenance ROI.