Reliability Centered Maintenance(RCM): What It Is, Best Practices and More
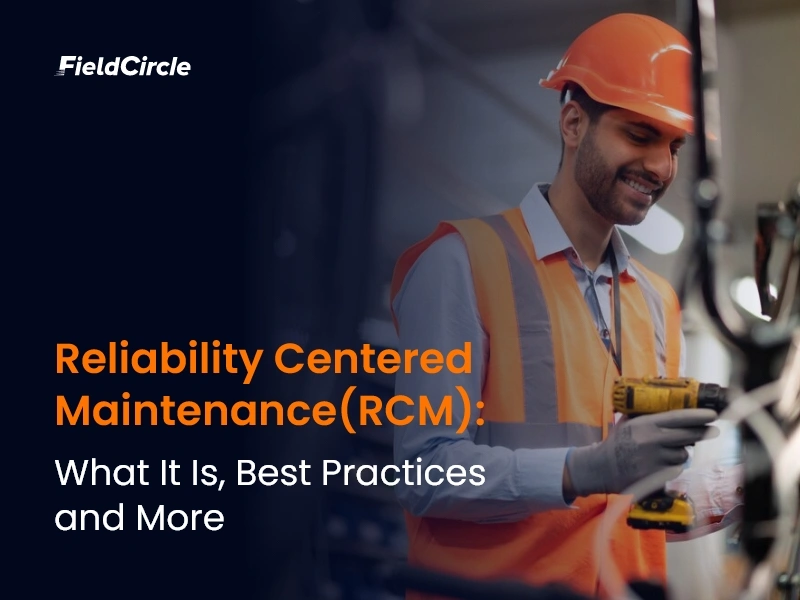
Unplanned equipment downtime is a formidable adversary for industries. “Value of Reliability” survey by ABB revealed that over two-thirds of industrial businesses experience unplanned outages at least once a month, with each hour of downtime costing approximately $125,000.
These staggering figures underscore a critical need for maintenance managers to enhance equipment reliability while controlling costs. Traditional maintenance approaches, such as reactive (“fix it when it breaks”) and time-based preventive maintenance, often prove inadequate. Reactive maintenance processes lead to unpredictable downtime and inflated expenses, while time-based approaches can result in unnecessary interventions, wasting resources and potentially introducing new issues.
To navigate these challenges, many organizations are turning to a Reliability-Centered Maintenance program. Let’s delve into it further.
What is Reliability-Centered Maintenance Strategy?
Reliability-Centered Maintenance (RCM) is a systematic approach aimed at ensuring that systems continue to perform their intended functions within their operational context. Originating in the aviation industry in the 1960s, RCM has since been adopted across various sectors to enhance the efficiency of maintenance management by sustaining equipment reliability and performance.
At its core, RCM seeks to balance the maintenance costs with the consequences of failure, focusing on preserving system functions, identifying failure modes, and prioritizing maintenance tasks based on their impact on overall system reliability. By implementing RCM, organizations can significantly reduce their dependence on emergency maintenance, ensuring that equipment failures do not result in costly disruptions.
What are the Key Questions Surrounding Reliability-centered Maintenance (RCM)?
RCM strategy follows a structured decision-making process based on seven fundamental questions (as outlined by the SAE JA1011 standard). These questions framed by the Society of Automotive Engineers (SAE) under Decision, Analysis, and Action help maintenance teams assess asset reliability and determine optimal maintenance strategies.
Decision (Defining the problem and scope)
- What are the asset’s primary functions and performance standards?
Every asset has a primary function (e.g., a pump moves fluid) and secondary functions (e.g., operating within a certain temperature range). Clearly defining these ensures maintenance needs align with operational needs.
- How can the asset fail to perform its functions?
This involves identifying failure modes, such as mechanical breakdown, loss of efficiency, or unexpected shutdowns. Each failure mode must be documented to understand potential risks.
Analysis (Understanding failure mechanisms and consequences)
- What causes each failure mode?
Failure modes have specific causes, such as wear and tear, operator errors, environmental factors, or manufacturing defects. Understanding these causes helps in selecting the right preventive measures.
- What happens when a failure occurs?
This question examines the impact of each failure, ranging from minor inefficiencies to catastrophic system breakdowns. Knowing the consequences helps prioritize maintenance actions.
- What are the consequences of failure?
Failures impact safety, operations, environment, and costs. For example, a failure in a power plant could lead to worker injuries, production loss, or regulatory violations.
Action (Implementing maintenance and mitigation strategies)
- What can be done to predict or prevent failure?
RCM evaluates maintenance strategies, such as:
- What should be done if failure cannot be prevented?
Some failures are unpredictable or too costly to prevent. In such cases, organizations implement:
- Failure management strategies, such as running assets to failure (acceptable in non-critical assets).
- Redundant systems, like backup generators in power plants.
Predictive maintenance (PdM) strategy – Using condition monitoring to detect failures before they happen.
Preventive maintenance strategy– Regular servicing based on failure patterns obtained from maintenance history.
Redesign or modification – Improving asset design to eliminate failure modes.
Use Combination of strategies – Use condition-based and preventive maintenance strategies to nip the problems in the bud.
What are the Benefits of Reliability-centered Maintenance (RCM)?
Listed are the important benefits of reliability centered maintenance. They are deeply rooted in what RCM aims to achieve and how it redefines the maintenance strategy from a reactive, blanket approach to a more precision-driven, proactive maintenance system.
-
Systematic Identification of Vulnerabilities
RCM identifies and addresses the weakest points in an equipment system by analyzing failure modes and potential consequences. This allows businesses to address reliability weaknesses before they escalate, improving overall system stability and avoiding sudden breakdowns. RCM ensures that maintenance efforts focus on the most vulnerable components, reinforcing the entire system’s reliability.
-
Better prevention of Critical Failures
RCM helps businesses pinpoint the most critical failure modes for each piece of equipment. By focusing on high-priority assets and addressing potential issues before they occur, RCM minimizes the risk of catastrophic breakdowns. This proactive approach enhances equipment reliability, keeping key machinery functioning smoothly and reducing operational disruptions.
-
Lesser Reactive Work
By moving away from reactive maintenance, RCM emphasizes preventive and predictive strategies. It focuses on identifying potential issues and addressing them before they turn into failures.
-
Optimized Uptime
By using data-driven techniques, RCM predicts when equipment is likely to fail. This enables companies to schedule maintenance before a failure happens, reducing the risk of unintended downtime.
-
Operational Continuity
RCM prioritizes the most reliable operational conditions for equipment which leads to more consistent daily operations and minimal disruptions, ultimately boosting productivity. Reliable equipment means smoother workflows, fewer interruptions, and greater operational efficiency across the board.
-
Ongoing Reliability Evaluation
As equipment performance evolves, RCM continuously assesses its condition and adjusts maintenance actions accordingly. By regularly evaluating reliability, organizations ensure that maintenance activities remain aligned with the equipment’s changing needs, leading to sustained operational reliability and adaptability over time.
-
Smarter Maintenance Budgeting
RCM helps businesses allocate resources more efficiently by focusing maintenance efforts on high-risk, reliability-critical assets. The method reduces unnecessary expenditures on low-priority equipment while directing funds to areas that directly impact reliability, thereby contributing in significant cost savings.
-
Reduction of Maintenance Backlog
By addressing maintenance needs in a structured, priority-based way, RCM prevents the accumulation of a maintenance backlog. With a focus on addressing problems before they escalate, RCM keeps maintenance schedules on track, reduces bottlenecks, and ensures that repairs and interventions are completed in a timely manner.
How to Implement Reliability-centered Maintenance (RCM)?
Implementing reliability-centered maintenance (RCM) follows a structured process to evaluate system functions, identify potential failures, and establish the most suitable maintenance strategies. Follow these steps to implement RCM effectively:
-
Define Objectives and Scope
Start by establishing clear objectives for the RCM program, such as improving asset reliability, minimizing downtime, or reducing maintenance costs. The next task is to define the scope by identifying the assets or systems that will be analyzed. Prioritize assets based on their criticality to safety, production, and operational efficiency. For example, key equipment such as pumps, motors, or safety-critical systems should be at the forefront of the analysis.
-
Develop an RCM Plan
Once the objectives and scope are set, create a detailed RCM plan. This plan should outline the approach to be followed, including key roles and responsibilities, timelines, and required resources. The plan will also define the methodology for conducting failure analysis, establishing maintenance strategies, and determining performance metrics. This step ensures alignment with overall organizational goals and readiness for execution.
-
Assemble the RCM Team
Next, form a cross-functional team. This team should include representatives from maintenance, operations, engineering, and reliability departments. The team will collaborate to identify system functions, failure modes, and consequences, benefiting from the diverse expertise and knowledge each member brings to the table. This cross-disciplinary approach ensures that all perspectives are considered in the RCM process.
-
Identify Critical Assets and Functions
Now, create an asset inventory that outlines the functions, performance expectations, and operational significance of each asset. Based on this inventory, prioritize assets by criticality, focusing first on those that are essential to safety, production, and overall efficiency. For instance, assets that directly influence production capacity, like turbines or pumps, should receive higher attention than less critical components.
-
Perform Failure Mode and Effect Analysis (FMEA)
In this step, perform Failure Mode and Effect Analysis (FMEA) for each critical asset. Identify potential failure modes and evaluate the consequences of these failures. Classify failure modes based on their severity, frequency, and the likelihood of occurrence, using a risk matrix to prioritize those with the highest potential impact. For example, a mechanical failure in a critical pump could halt production, while an electrical fault in a non-essential lighting system may have minimal impact.
-
Develop Maintenance Strategies
Based on the results of the FMEA, determine appropriate maintenance strategies for each asset. These strategies can include preventive maintenance for routine tasks, predictive maintenance (PdM) for tasks based on asset condition (e.g., vibration monitoring), and corrective maintenance (CM) for reactive tasks after a failure. The chosen strategy should align with the risk level identified in the FMEA to mitigate the most critical failures efficiently.
-
Create Detailed Maintenance Plans
Following the maintenance strategy development, create appropriate maintenance tasks for each asset, detailing their frequency, procedures, and required resources. The plan should be tailored to each asset’s criticality and failure risk. Use historical data, such as previous breakdowns, to refine maintenance intervals and prioritize tasks. For example, a high-risk motor may require more frequent inspections, while a less critical air conditioner may only need annual checks.
-
Implement the Maintenance Plan
With the plan in place, begin executing the maintenance tasks according to the established schedule. Ensure that maintenance staff has access to the necessary tools, parts, and training. Implement and leverage asset management software to track task completion, manage work orders, and monitor asset performance. For example, if a pump is scheduled for a predictive maintenance check, ensure the vibration analyzer is ready and staff is trained to interpret the data.
-
Train and Build Awareness
To support the successful implementation of RCM, provide comprehensive training to all maintenance staff. This includes training on the new maintenance strategies, tools, and the rationale behind the RCM decisions. Ensuring that personnel understand the purpose of the maintenance tasks helps to align the team’s efforts and improve task execution efficiency. For instance, training on using condition-monitoring equipment can help technicians identify early signs of failure.
What are the Best Practices for Implementing Reliability-centered Maintenance (RCM)?
Reliability-Centered Maintenance (RCM) is a powerful approach for ensuring the long-term performance and reliability of systems, particularly in industries like manufacturing, energy, and transportation. To implement RCM effectively, you need a set of practices that go beyond simple, generic steps and are tailored to your specific operational needs. These best practices are:
-
Assess Failure Consequences, Not Just Causes
Looking at failure causes alone is like treating symptoms without diagnosing the disease. Evaluate how failures affect operations, safety, and costs. This approach helps direct maintenance efforts toward the most business-impacting issues instead of wasting time on minor setbacks.
-
Set Priorities Based on Business Impact
Some failures barely make a dent, while others bring operations to a grinding halt. Rank assets and failure modes based on how much they affect production, revenue, and safety. Addressing high-priority risks first keeps the business running without unnecessary slowdowns.
-
Use Condition-Based Maintenance Where It Matters
Not every asset needs routine servicing and here you need to use condition-based maintenance. For equipment with unpredictable failure patterns, monitoring real-time performance data beats rigid maintenance schedules. Sensors and analytics provide insights, allowing maintenance teams to act only when needed, cutting unnecessary work.
-
Refine Preventive Maintenance with Failure Data
Sticking to fixed maintenance intervals without data is like changing car tires every six months, whether they’re worn out or not. Use failure records to fine-tune schedules, reducing wasteful maintenance while keeping essential equipment in top shape.
-
Break Down Organizational Silos
Maintenance, operations, and engineering teams working in isolation create more problems than they solve. Establish open communication channels so insights from real-world equipment performance drive maintenance decisions, preventing teams from working at cross-purposes.
-
Optimize Spare Parts Inventory Without Overstocking
Stocking every possible spare part ties up cash, while running out of essentials brings maintenance to a standstill. Use historical failure data and usage patterns to keep just the right parts on hand, avoiding unnecessary inventory buildup.
-
Automate Data Collection to Eliminate Guesswork
Relying on manual logs and operator memory leads to gaps in failure tracking. Automated data collection tools provide accurate, real-time insights into asset health, helping teams catch patterns and prevent breakdowns before they happen.
-
Analyze Maintenance Effectiveness and Adjust Regularly
A maintenance plan isn’t a “set it and forget it” deal. Regularly reviewing failure rates, downtime trends, and repair costs helps fine-tune strategies. Adjusting based on real-world performance keeps RCM relevant and effective.
-
Make Root Cause Analysis a Standard Practice
Fixing recurring failures without identifying the root cause is like bailing water out of a sinking boat without plugging the hole. Every breakdown should lead to an investigation that digs deep enough to prevent the same issue from cropping up again.
-
Leverage Predictive Analytics for Smarter Maintenance
Guessing when a failure will happen is a thing of the past. Advanced analytics tools process historical and real-time data to forecast issues before they turn into costly breakdowns. This approach shifts maintenance from reactive to proactive.
-
Develop a Culture of Reliability
A reliable system isn’t just about machines—it’s about people. Encourage employees at all levels to take ownership of system reliability. When teams collaborate, share insights, and focus on long-term performance, maintenance becomes a shared responsibility rather than an afterthought.
-
Integrate RCM with Other Business Processes
Treating RCM as a standalone process limits its impact. Connect maintenance strategies with broader business goals such as cost management, sustainability, and operational efficiency. When RCM supports overall business objectives, it adds long-term value instead of being just another expense.
-
Utilize Software for RCM Analysis
Manual tracking leaves too much room for error. A computerized maintenance management system (CMMS) streamlines failure mode analysis, predictive maintenance, and reporting. Automated tracking and analytics reduce guesswork, keeping maintenance teams on top of schedules and performance trends without unnecessary hassle.
-
Incorporate Reliability Growth Techniques
Reliability isn’t a one-time fix—it’s a process. Learn from past failures, tweak designs, and adjust procedures to reduce future breakdowns. A system that adapts and evolves over time becomes stronger, cutting long-term costs while keeping operations running smoothly.
What are the Examples of Reliability-centered Maintenance (RCM)?
Reliability-Centered Maintenance (RCM) is applied across various industries to optimize maintenance strategies and improve system reliability. Following are some examples of RCM in practice:
- Aviation Industry
Airlines keep aircraft engines in check with RCM, relying on sensors and predictive analytics to catch problems early. Engineers step in before small issues turn into major failures. Planes stay in service without last-minute maintenance throwing flight schedules into disarray.
- Power Generation
Gas turbines don’t last long without constant monitoring. Power plants use RCM to track vibration, temperature, and pressure shifts, spotting wear before it leads to breakdowns. Engineers replace or repair parts right on time, avoiding sudden failures that could knock power grids offline.
- Manufacturing Industry
Automakers use RCM to keep robotic arms and conveyor belts from breaking down. Sensors track speed, torque, and energy use, flagging even the slightest irregularities. Maintenance teams get ahead of potential failures, keeping production lines from grinding to a halt.
- Oil and Gas Industry
Offshore drilling equipment takes a beating under tough conditions. RCM helps crews catch early signs of wear in blowout preventers and drilling motors. Addressing problems before they escalate prevents shutdowns, reduces safety risks, and keeps operations from running into costly delays.
- Rail Transportation
Rail operators stay ahead of mechanical failures by using RCM to track wheel wear, braking systems, and track alignment. Automated systems catch defects early, letting maintenance teams make repairs before trains fall behind schedule or, worse, become safety hazards.
- Healthcare Industry
Hospitals rely on RCM to keep MRI and CT scanners running without unexpected failures. Engineers track performance data to catch faults before they disrupt patient care. Medical staff continue diagnoses without delays, and hospitals avoid the hassle of unplanned equipment downtime.
How does FieldCircle Maintenance Software aid in RCM Implementation?
Reliability-centered maintenance remains an important maintenance strategy to build a fool-proof and effective maintenance program. It extends beyond routine maintenance and requires a mix of predictive, preventive, and corrective strategies to keep assets functioning efficiently.
FieldCircle maintenance software strengthens RCM by providing the necessary infrastructure to execute, monitor, and refine maintenance strategies effectively. It acts as a lever to amalgamate different maintenance techniques. And most importantly, by offering all essential functionalities under one umbrella, our tool enables organizations to build a maintenance ecosystem that aligns with reliability goals.