What is Risk-based Maintenance? Everything You Should Know
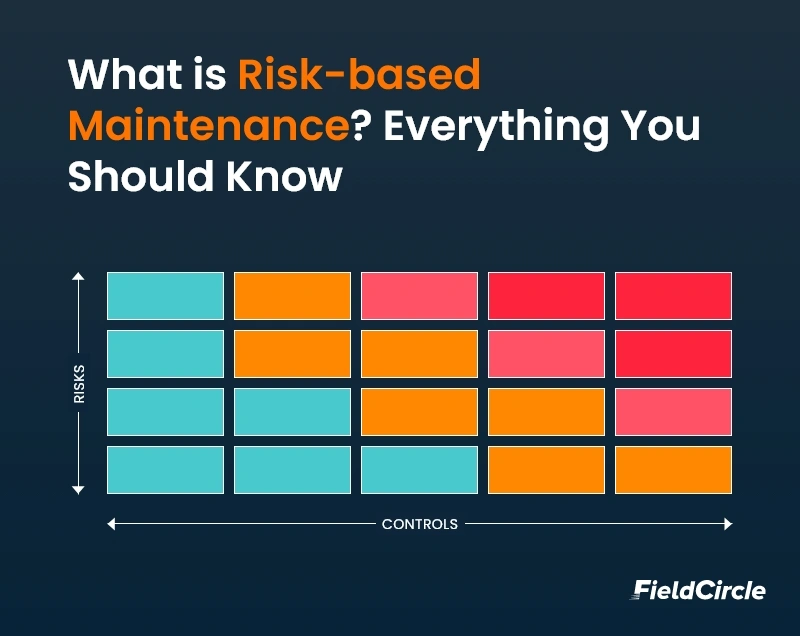
What happens when a key piece of equipment fails without warning? Production grinds to a halt, deadlines get missed, and repair costs pile up. Maintenance teams rush to fix the issue, but by then, the damage is done.
Traditional maintenance strategies either wait for things to break or follow rigid schedules that don’t always match real-world conditions. Some machines get serviced too frequently, while others fail unexpectedly, throwing everything into chaos.
Risk-based maintenance flips the script. Instead of treating every asset the same, it zeroes in on the equipment that poses the biggest threat to operations.
This blog dives into the fundamentals of RBM, exploring how risk assessments and data analysis drive decisions about which assets need attention and when. We look at essential things surrounding RBM like its importance, the steps and best practices to implement it, the role of CMMS in its implementation and how to use it. Let’s begin.
What is risk-based maintenance (RBM)?
Risk-based maintenance (RBM) is a maintenance approach that prioritizes maintenance tasks by evaluating the probability and consequences of equipment failure. It focuses on assessing risks, identifying key assets, and allocating resources effectively. In this maintenance strategy, high-risk components receive attention first, which reduces unnecessary work on low-risk machinery while sustaining operational efficiency and meeting safety standards.
What is the Importance of Risk-based Maintenance?
The following reasons highlight why risk-based maintenance is a key part of a maintenance program for any business.
-
Fixing What Actually Matters
-
Avoiding Wasteful Maintenance Work
-
Preventing Failures from Causing a Domino Effect
-
Cutting Down on Human Errors
-
Making Smarter Use of Maintenance Budgets
-
Keeping the Most Important Equipment Running
Not every machine needs constant attention, but some failures can shut down an entire operation. Risk-based maintenance helps businesses focus on assets that, if they fail, could cause serious financial losses or safety hazards. Instead of servicing everything equally, it prioritizes the equipment that poses the highest risks.
More than half of businesses spend around 30 hours a week in maintenance. They stick to fixed schedules, replacing parts or servicing equipment even when it’s unnecessary. That approach eats up time, money, and manpower and they are forced to operate with limited resources. Risk-based maintenance moves away from routine check-ups and instead uses real data to determine when intervention is actually needed.
In complex systems, a single malfunction can trigger failures in other connected machines. A risk-based strategy identifies weak links before they cause a ripple effect. Addressing these points early keeps everything running smoothly and prevents bigger, costlier breakdowns. Notably, a chemical plant in gulf coast reduced maintenance cost by a whopping USD 3.2 million using risk-based strategies.
Believe it or not, unnecessary maintenance can create new problems. Every time a machine is opened up for servicing, there’s a chance of improper reassembly, contamination, or even accidental damage. By reducing unnecessary work, risk-based maintenance lowers the chances of technicians unintentionally causing failures.
Throwing money at every possible issue isn’t sustainable, especially when you are amongst those 42.5% of enterprises that allocate 21-40% of their operating budget on maintenance and cleaning. Instead of spreading resources thin by maintaining everything at the same frequency, risk-based maintenance helps businesses invest in the areas that need it the most. That means fewer wasted hours and lower maintenance costs overall.
Some assets are more valuable than others, especially those tied directly to production or compliance requirements. Risk-based maintenance zeroes in on these high-priority machines, making sure they stay operational while secondary equipment gets serviced as needed.
Steps to implement Risk-based Maintenance (RBM)
Following are the steps that you must follow to implement a risk-based maintenance strategy. Each step has been explained by offering real-life insights into how it is unfolded and how the steps combined together drive the implementation.
1. Collect Data
A data-driven approach is fundamental to RBM. Organizations gather asset-related data from multiple sources to assess current conditions, predict failures, and allocate maintenance resources effectively.
- Historical failure data is extracted from CMMS (Computerized Maintenance Management Systems), which provides data around key maintenance metrics like Mean Time Between Failures (MTBF) and Mean Time To Repair (MTTR) statistics.
- Condition monitoring data from IoT sensors, SCADA systems, and thermal imaging provides real-time performance insights.
- Operational parameters such as temperature, vibration levels, and load cycles are recorded to assess asset stress levels.
To maintain consistency, collected data is structured into a centralized repository. Below is an example of how organizations organize asset performance records:
Asset ID | Failure Mode | MTBF (Hours) | MTTR (Hours) | Condition Data | Environmental Factors |
---|---|---|---|---|---|
Motor-001 |
Overheating |
15,000 |
6 |
Temp: 85°C |
High humidity |
Pump-002 |
Bearing Wear |
12,500 |
5 |
Vibration: 1.5 mm/s |
Corrosive exposure |
Conveyor-003 |
Belt Slippage |
10,000 |
4 |
Load Variance: 10% |
High dust levels |
Chiller-004 |
Refrigerant Leak |
14,000 |
7 |
Pressure Drop: 5% |
Extreme temperature fluctuations |
Generator-005 |
Battery Failure |
9,500 |
8 |
Charge Level: 60% |
Frequent power surges |
Automating data collection through APIs and cloud-based monitoring systems eliminates manual errors and inconsistencies, allowing maintenance teams to make data-driven decisions.
2. Determine Asset Criticality
Not all assets contribute equally to operations. Organizations classify assets based on their impact on productivity, safety, and costs. The most critical ones require priority maintenance planning, while non-essential equipment receives routine or minimal attention. You must identify assets that carry the most risk.
A Criticality Score (on a scale of 0–10) is assigned to each asset based on:
- Operational Impact – How failure disrupts production.
- Safety & Compliance Risks – Potential hazards or regulatory violations.
- Financial Impact – Costs of repair, replacement, and downtime.
Asset | Operational Impact (0-10) | Safety Risk (0-10) | Financial Impact (0-10) | Total Score (0-30) |
---|---|---|---|---|
Boiler A |
9 |
8 |
10 |
27 |
HVAC Unit |
4 |
2 |
5 |
11 |
Main Conveyor |
10 |
7 |
9 |
26 |
Cooling Tower |
8 |
6 |
7 |
21 |
Emergency Generator |
10 |
9 |
10 |
29 |
Assets scoring above 20 are deemed high-priority, requiring immediate risk assessment. Lower-scoring assets undergo standard maintenance protocols.
3. Determine Failure Likelihood
The probability of failure varies across assets and is influenced by:
- Historical Failure Rates – Derived from MTBF records.
- Current Performance Metrics – Anomalies detected via vibration, temperature, or ultrasonic monitoring.
- Environmental Stressors – Exposure to moisture, corrosive chemicals, or extreme temperatures.
A Failure Likelihood Index is calculated using:
Asset | Expected Lifecycle (Years) | Age (Years) | Recent Failure Rate (%) | Industry Standard Failure Rate (%) | Failure Likelihood Index (0-1) |
---|---|---|---|---|---|
Boiler A |
20 |
15 |
12 |
8 |
0.9 |
HVAC Unit |
12 |
8 |
5 |
6 |
0.5 |
Main Conveyor |
18 |
10 |
9 |
7 |
0.75 |
Cooling Tower |
15 |
6 |
6 |
6 |
0.6 |
Emergency Generator |
25 |
12 |
15 |
9 |
0.95 |
4. Calculate Risk Priority
Once failure likelihood and asset criticality are determined, organizations calculate the Risk Priority Number (RPN) using:
Asset | Criticality Score | Failure Likelihood (0-1) | RPN Score | Risk Category |
---|---|---|---|---|
Boiler A |
27 |
0.9 |
24.3 |
High Risk |
HVAC Unit |
11 |
0.5 |
5.5 |
Low Risk |
Main Conveyor |
26 |
0.75 |
19.5 |
Medium Risk |
Cooling Tower |
21 |
0.6 |
12.6 |
Medium Risk |
Emergency Generator |
29 |
0.95 |
27.55 |
High Risk |
5. Analyze the Findings
With risk-prioritized assets identified, failure analysis is conducted using methodologies such as Root Cause Analysis (RCA) and Pareto Analysis to pinpoint recurring failure sources.
Failure Cause | Occurrences | Percentage of Total Failures |
---|---|---|
Bearing Wear |
35 |
38% |
Electrical Fault |
25 |
27% |
Lubrication Issues |
18 |
20% |
Misalignment |
14 |
15% |
This analysis enables targeted corrective actions, such as improved lubrication protocols or electrical insulation enhancements.
6. Prioritize Asset Failures
With risk priorities set, organizations allocate resources effectively. Typical actions include:
- Immediate Maintenance (RPN > 20) – Critical failures requiring urgent intervention.
- Preventive Maintenance (RPN 10-20) – Scheduled inspections based on risk exposure.
- Condition-Based Monitoring (RPN < 10) – Low-risk assets monitored periodically.
Risk Category | Recommended Action | Maintenance Frequency |
---|---|---|
High Risk |
Immediate corrective maintenance |
Within 24 hours |
Medium Risk |
Preventive maintenance |
Every 3 months |
Low Risk |
Condition monitoring |
Every 6 months |
7. Create a Risk Mitigation Plan
A structured plan outlines:
- Budget Allocation – Assigning funds based on asset priority.
- Technology Investments – Implementing AI-based monitoring for high-risk equipment.
- Reassessing Risk Scores Quarterly – Updating calculations as assets age.
- Training Teams on New Technologies – Ensuring maintenance staff adapt to AI-driven insights.
- Benchmarking Against Industry Data – Comparing asset performance with industry best practices.
- Adopt a structured risk assessment framework to quantify risks based on operational needs and asset failure consequences.
- Segment assets by their risk profiles to focus maintenance efforts on high-risk assets while minimizing unnecessary actions on lower-risk items.
- Use dynamic risk scoring based on real-time data to adjust maintenance priorities as operating conditions and asset performance evolve.
- Incorporate failure consequence analysis to evaluate both direct and indirect impacts of asset failure, including downtime and safety hazards.
- Make risk-based decisions data-driven, leveraging advanced analytics to predict failures and assess the cost-benefit of maintenance actions.
- Establish clear thresholds for action in your risk models, ensuring predefined maintenance actions trigger automatically when risk levels are exceeded.
- Incorporate multi-disciplinary input into risk assessments, drawing expertise from operations, maintenance, safety, and engineering.
- Customize risk strategies for different asset types, avoiding a one-size-fits-all approach to maintenance for various asset categories.
- Implement regular risk reviews to keep assessments up-to-date and reflect changes in asset health or operational conditions.
- Integrate risk-based metrics into maintenance performance indicators, such as cost per risk-mitigated failure, to evaluate the effectiveness of your approach.
- Utilize predictive maintenance with maintenance software for high-risk assets for meticulously addressing potential failures proactively before they occur.
- Prioritize training and upskilling of maintenance teams in risk-based methodologies, empowering them to make informed, data-driven decisions.
- Establish an asset lifecycle approach, where maintenance strategies adjust over time based on the asset’s changing risk profile.
- Implement a culture of continuous risk monitoring with automated alerts tied to real-time asset condition data, reducing response time to emerging risks.
- Leverage asset-specific reliability models to define optimal intervention points based on historical data and failure probabilities.
- Precise Risk Identification: The heart of risk-based maintenance is understanding which equipment poses the most significant threat to operations. CMMS pulls together historical data, asset conditions, and performance metrics. This data allows maintenance teams to quantify risk levels—not just the chance of failure but the real-world impact on safety, production, and costs if failure occurs. By using this data, CMMS offers a clear view of where attention is most needed, eliminating the guesswork in risk assessments.
- Data-Driven Prioritization: With risk-based maintenance, assets are not treated equally. CMMS enables a sharp focus on assets that, if they fail, would cause the most disruption. For example, CMMS can track the criticality of each piece of equipment and assess the consequences of its failure. It then prioritizes maintenance actions based on that data. This approach ensures that maintenance teams direct their efforts toward the equipment that presents the highest operational or financial risk, rather than spreading resources thinly across all equipment.
- Failure Prediction: Risk-based maintenance relies heavily on predictive techniques, and CMMS is built to support this. By analyzing real-time data from sensors and past failure trends, CMMS can identify patterns that signal an impending failure. With this early warning, maintenance teams can act before a critical breakdown occurs. Predictive maintenance in a risk-based framework reduces downtime and prevents major disruptions, aligning directly with risk management goals.
- Failure Mode and Effects Analysis (FMEA) Integration: One of the key components of RBM is understanding not just when equipment might fail, but how and why it fails. A CMMS integrated with FMEA tools allows maintenance teams to analyze failure modes in detail. It documents each potential failure scenario, assigns a risk ranking to it, and suggests appropriate mitigation steps. This creates a living document where teams can continually refine their approach based on lessons learned, making the maintenance strategy as targeted and effective as possible.
- Maintenance Task Optimization: Instead of performing unnecessary or over-frequent checks, a CMMS helps optimize maintenance tasks to match risk levels. The system schedules activities based on the actual wear and tear of equipment rather than sticking to predefined intervals. For instance, it won’t schedule inspections for an asset that’s low-risk unless a potential issue arises. This makes better use of time, manpower, and resources, all while keeping operational costs down.
- Resource Efficiency: CMMS helps allocate resources in line with risk priority, which prevents overstaffing or underutilization. For high-risk assets, the system ensures that skilled personnel are assigned, while less critical tasks are managed with less expertise, making the most of your team’s capabilities. This strategic approach allows you to act when and where it matters most.
- Continuous Feedback Loop: After implementing RBM, a CMMS collects data on the effectiveness of maintenance strategies. By analyzing the data on equipment performance and failure trends, the system can adjust its recommendations for future tasks, creating a feedback loop that constantly refines the maintenance process. This data-driven optimization helps move maintenance from a reactive model to one that’s fully based on minimizing risk and improving asset reliability.
-
Establish Asset Criticality and Risk Profiles
-
Integrate Condition Monitoring Data
-
Assign Risk-Based Maintenance Strategies
-
Automate Work Order Prioritization
- Leverage Predictive Analytics for Future Risk
-
Monitor Maintenance Effectiveness with Risk Metrics
-
Integrate Risk-Based Decision-Making in Workflow
-
Allocate Resources Efficiently Based on Risk
-
Continuous Risk Assessment and Adjustment
-
Review and Refine Strategy through Reporting
Workforce Planning – Ensuring skilled technicians handle critical assets.
For instance, if a factory’s primary boiler has a high RPN, the organization may invest in redundant backup systems to mitigate failure risks.
8. Continuously Improve
RBM is an ongoing process. Organizations refine their strategies by:
A well-implemented RBM strategy transforms maintenance from reactive to proactive, leading to lower costs, reduced downtime, and extended asset lifespan.
Best Practices to implement Risk-based Maintenance (RBM)
Below are key best practices that must be followed for the successful implementation of risk-based maintenance and facilitate a cost-effective and efficient approach to asset management.
How does CMMS help implement Risk-based Maintenance (RBM)
A computerized maintenance management system (CMMS) is indispensable when implementing risk-based maintenance (RBM) because it turns reactive maintenance into a strategic, risk-oriented approach. Rather than maintaining equipment based on arbitrary schedules or time intervals, a CMMS takes a more granular approach by focusing on the actual risk of failure. With its ability to track data, prioritize high-risk equipment, and ensure proper resource allocation, a CMMS becomes the backbone of a solid risk-based strategy. Here’s how it plays a decisive role in the successful application of RBM:
How to implement Risk-based Maintenance (RBM) using a CMMS
Following are the steps to systematically configure and use a CMMS for a resilient risk-based maintenance strategy.
Begin by categorizing assets in the CMMS based on their criticality (safety, production impact). Assign each asset a risk profile using a matrix that combines likelihood and consequence of failure. This will help prioritize which assets require the most attention.
Next, integrate real-time condition monitoring (e.g., vibration, temperature sensors) with your CMMS. This allows the system to continuously track asset health and update risk profiles based on real-time data, ensuring the system reflects current asset conditions for more accurate maintenance planning.
With the risk profiles in place, configure your CMMS to automatically assign maintenance strategies for each asset. High-risk assets may require predictive or condition-based maintenance, while lower-risk assets can follow standard preventive schedules. Using preventive maintenance software helps adjust schedules dynamically based on changing conditions.
When a work order is generated, the CMMS should use the asset’s risk level to automatically prioritize tasks. High-risk work orders are flagged for immediate action, and resources are allocated based on asset importance, ensuring critical issues are dealt with first.
As part of your ongoing strategy, use predictive analytics within the CMMS to analyze trends in failure data. This allows the system to forecast potential issues before they arise, which can be used to preemptively adjust asset risk profiles and maintenance schedules to avoid unexpected downtime.
Track key performance indicators (KPIs) like Mean Time Between Failures (MTBF) and Mean Time to Repair (MTTR) for each asset in the CMMS. These metrics help you evaluate the effectiveness of your risk based approach, ensuring that the right assets are receiving the correct level of maintenance.
As maintenance work progresses, use the CMMS to ensure risk-based decision-making is integrated into workflows. For high-risk assets, workflows should prompt faster approvals and assign specialized personnel, ensuring critical maintenance tasks receive the urgency and expertise they require.
Ensure that resources (such as skilled labor and parts) are allocated according to asset risk. Use the CMMS to automatically prioritize high-risk assets for resource allocation, ensuring your maintenance team focuses on what matters most while optimizing costs and preventing unnecessary downtime.
Regularly reassess asset risk profiles using real-time condition data and maintenance feedback. Adjust risk levels in the CMMS based on new information—such as performance changes or failure occurrences—and modify the maintenance approach accordingly to stay proactive.
Finally, use CMMS reports to conduct regular reviews of your risk-based maintenance strategy. Analyze the maintenance data to identify trends, areas for improvement, and whether the current risk levels and maintenance schedules are yielding the desired results. Adjust the strategy for continual improvement.
Assess Risk and Improve Maintenance with FieldCircle CMMS
FieldCircle’s CMMS software transforms maintenance management by embedding risk assessment into decision-making. It shifts focus from routine servicing to prioritizing assets based on failure impact, aligning maintenance efforts with business goals. With structured asset intelligence, organizations allocate resources effectively, eliminating unnecessary interventions while addressing high-risk components before disruptions occur.
At a strategic level, the system fosters accountability and consistency in maintenance execution. Standardized policies replace ad-hoc practices, creating a structured framework for long-term asset reliability.